聚苯胺在环氧树脂涂层中防蚀性能研究
时间:2014-03-30 14:44来源:中山大桥化工集团有限公司 作者:傅文峰,戈成岳
0 前言
导电聚合物被认为对铁基金属能够提供电化学保护作用,在导电聚合物中,聚苯胺由于电化学性质稳定,而且原料易得,制备过程简单,成为研究的热点。但是,聚苯胺欠佳的溶解性和加工性能限制了其实际应用,一般将聚苯胺与环氧
树脂共混配成复合涂料。由于聚苯胺独特的导电性能,复合涂层除对被保护基体提供屏蔽作用外,还能提供有效的电化学保护。本文分别在“高强酸—硫酸”和“中强酸—磷酸”体系中采用直接混合氧化法制备了掺杂态聚苯胺,通过机械研磨把聚苯胺分散到环氧
树脂中,利用电化学阻抗谱和盐雾试验研究了在Q235钢基体上聚苯胺的防蚀性能。
1 试验部分
1.1 试剂与仪器
苯胺、过硫酸铵、硫酸、磷酸 ,分析纯;环氧树脂(E-20)、固化剂(聚酰胺),工业品。85-2A磁力搅拌器,DHG-9145A电热鼓风干燥箱,JSF-400高速分散机,SK-450振动式混合机(Fast& Fluid),PARSTAT2273电化学工作站,BGD880盐雾试验箱。
1.2 聚苯胺的合成
将一定量的苯胺和过硫酸铵分别溶于浓度为1.0mol/L的掺杂酸溶液中;然后将两份溶液迅速混合,充分搅拌,20 ℃下静置反应24 h。将所得产物分别用去离子水和乙醇清洗至中性,分离、干燥后得到墨绿色掺杂态聚苯胺产物。
1.3 聚苯胺-环氧树脂复合涂料的制备
首先将一定量的聚苯胺、环氧树脂和溶剂预分散,浸泡放置一夜后加入一定量的玻璃珠用振动混合机研磨2~3遍(一遍20 min),每研磨一遍后降温再进行下一遍。研磨完成分别用120目和200目的铜网依次过滤,最后用400目绢布过滤得环氧树脂与聚苯胺研磨组分,使用时与固化剂按一定比例充分混合。
1.4 电化学测试与盐雾试验
用400~1 000目砂纸逐级打磨直径为10 mm的Q235钢电极,清洗、除油、干燥,涂覆加入固化剂的聚苯胺-环氧树脂复合涂料,自然干燥,制得膜厚为(60±5) μm的工作电极。采用三电极测试系统在3.5%的氯化钠溶液中利用PARSTAT2273电化学工作站进行交流阻抗测试,其中辅助电极为铂电极,参比电极为饱和甘汞电极。用80目砂纸打磨150 mm×70 mm的Q235钢样板,清洗、除油、干燥后喷涂加入固化剂的聚苯胺-环氧树脂复合涂料,自然干燥,控制膜厚为(100±10)μm。在样板底部划痕后置于盐雾试验机中,试验周期为1 000 h。
2 结果与讨论
2.1 聚苯胺对环氧树脂成膜性能的影响
选择磷酸体系中制备的聚苯胺,改变聚苯胺的用量,研磨配制不同聚苯胺含量的聚苯胺-环氧树脂复合涂料,表1是添加不同用量的聚苯胺所得环氧树脂涂层的成膜情况。
由表1可以看出,当添加量不超过0.8%(质量分数)时,聚苯胺在环氧树脂中具有良好的分散性,随着聚苯胺用量的增加,涂层颜色逐渐加深,当聚苯胺用量为0.6%~0.8%时,涂层呈现蓝黑色,表面致密有光泽,成膜状态良好;当聚苯胺添加量达到1.0%时,涂层出现一定的粗糙度,光泽度受到影响;当聚苯胺用量达到2%时,涂层已有肉眼可见的
缩孔,致密性受到破坏;当聚苯胺用量达到4%时,缺陷已经非常明显,有大面积花斑出现。由此可见聚苯胺的添加量影响环氧树脂的成膜性能。在试验过程中还发现,添加聚苯胺后涂层的干燥速度显著变慢,而聚苯胺添加量越大,所需干燥时间越长。可能是由于聚苯胺具有很强的吸湿性,影响固化干燥,且聚苯胺的纳米纤维结构也影响树脂与固化剂的交联。
2.2 聚苯胺用量对防蚀性能影响的电化学研究
通过交流阻抗谱(EIS)研究涂层防蚀性能是一种快捷、有效的方法。图1和图2分别是不同聚苯胺添加量复合涂层在浸泡前和典型添加量的几组样品在浸泡7 d后的奈奎斯特图。
对于浸泡初期无扩散的奈奎斯特图,选择等效电路Rs(RcQc)进行拟合,如图3所示,图中Rs为溶液电阻,Qc为涂层电容,Rc为涂层电阻;对于浸泡7 d后存在显著扩散特征的奈奎斯特图,选择等效电路Rs(Qc(Rpo(Cd1(RtW))))进行拟合,如图4所示,图中Qd1为双电层电容,Rpo为通过涂层微孔途径的电阻值,Rt为电荷转移电阻,Zw为韦伯阻抗。
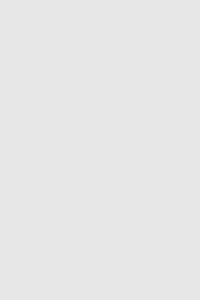
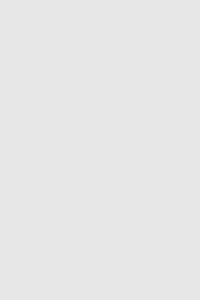
表2和表3为拟合所得参数及结果。
由图1和表2可以看出,与单纯环氧树脂相比(Rc=1.339×10
9),添加聚苯胺后,复合涂层的Rc普遍增加,当聚苯胺添加量为0.6%时,涂层电阻增加最大(Rc=5.117×10
9),这说明聚苯胺的加入提高了涂层的屏蔽保护效果;但当聚苯胺添加量达到2%时,浸泡开始就出现扩散迹象,可能由涂层致密性差造成。浸泡7 d后,图2和表3显示,添加量为0.6%的涂层电阻依然非常高(Rc=3.054×10
9),出现钝化膜特征,而纯环氧树脂涂层失效比较快,涂层电阻明显下降(Rpo=2.284×10
9),再次证明聚苯胺的加入对涂层保护效果的提高;另外,聚苯胺添加量为1.0%的涂层,浸泡7 d后涂层电阻下降更多(Rpo=1.456×109),并没有出现钝化迹象。可能的原因是聚苯胺在环氧树脂中分散限制导致添加量大的涂层致密性变差,大量的Cl-容易渗透进涂层底部使原本形成的钝化膜遭受破坏,从而失去保护作用。阻抗谱研究结果进一步证明聚苯胺在环氧树脂中合适的添加量不能超过1%,优选0.6%。
2.3 掺杂酸对聚苯胺防蚀性能影响的盐雾试验研究
盐雾试验是直观评价涂层失效的一种方法,用在海洋环境中的涂料,耐盐雾腐蚀是一项重要的性能,固定聚苯胺的添加量为0.6%,考察不同掺杂酸对复合涂层耐盐雾性能的影响。
图5和图6显示,盐雾试验168 h之内各涂层基本没有明显锈迹出现,仔细对比发现,磷酸掺杂的聚苯胺复合涂层效果更好一些;随着盐雾试验的进行,锈迹开始出现并不断增多,360 h时锈迹已经非常明显;继续试验,锈迹继续加重,720 h时各涂层之间保护性能优劣差别已经非常明显:磷酸掺杂的聚苯胺复合涂层保护效果明显优于硫酸掺杂的聚苯胺复合涂层。盐雾试验1 000 h后,把划痕部位进行剥离发现磷酸掺杂的聚苯胺复合涂层对基体仍然具有一定的附着力,而硫酸掺杂的聚苯胺复合涂层对基体基本失去附着力,容易成块剥落。剥离之后的照片更能清楚地说明保护效果的优劣,被磷酸掺杂的聚苯胺复合涂层保护的基体仍然光亮洁净,仅在划痕部位出现些微侵蚀,且已出现钝化迹象;被硫酸掺杂的聚苯胺复合涂层保护的基体在划痕部位遭到严重腐蚀,锈迹斑斑,其他部位也有腐蚀介质侵蚀痕迹。可能的原因有以下几种推测:(1)聚苯胺的形貌影响其在环氧树脂中的分散性,在高强酸—硫酸体系中合成的聚苯胺为规则的长纤维形貌,分散性能不如在中强
酸—磷酸体系中合成的不规则短纤维形貌的产品;(2)掺杂酸阴离子影响涂层与基体的结合强度,PO43-的存在提高了环氧树脂与基体的附着力;(3)掺杂酸阴离子影响复合涂层的催化钝化等电化学保护性能,众所周知,PO43-对铁基体有良好的钝化功能。
3 结语
通过振动混合机研磨把两种酸体系中合成的掺杂态聚苯胺分散到环氧树脂中。研究发现,聚苯胺的加入延长了环氧树脂涂层的成膜干燥时间,聚苯胺加入量越大所需干燥时间越长,涂层的表面光泽度也下降;交流阻抗谱研究发现,在合适的添加量下,聚苯胺加入到环氧树脂中对Q235钢能够提供有效的屏蔽保护和钝化保护,合适的添加量优选0.6%;盐雾试验结果表明:磷酸掺杂的聚苯胺复合涂层可以对基体提供好的保护,硫酸掺杂的聚苯胺复合涂层保护效果较差。
本站仅提供存储服务,所有内容均由用户发布,如发现有害或侵权内容,请
点击举报。