题 目 奥迪汽车加油盖板
的注塑工艺与模具设计
专 业 高分子材料与工程
学生姓名
学 号
指导教师
论文字数
完成日期 2018年5月
摘 要
本文分析了关于奥迪汽车加油盖板的成型特点,设计了一副含有斜顶杆的注塑模具,斜顶杆在对应的斜顶杆固定板中侧向滑动,斜顶杆与斜顶杆耐磨板配合?靠推板从下而上给斜顶杆一个推力推动斜顶杆向上运动后一段距离,斜顶杆在耐磨板和推板推力下,不仅向上运动了,并且向其倾斜方向运动了一段距离,既有推出又有侧抽作用;采用潜伏羊角浇口的注射模具,其特点是浇口凝料和塑件可自动分离;无需对浇口位置进行另外处理;不会在塑件外观面产生浇口痕迹?该模具设计的关键是分配好斜顶杆的行程及顶出的行程,以便有足够的顶出量来顶出产品?在制造方面,运用了氮化处理,淬火处理,从而提高零件性能?
关键词:汽车加油盖板;注塑模具;斜顶机构;潜伏浇口
ABSTRACT
This paperanalyzes the forming characteristics of the Audi car refueling cover plate. Apair of injection moulds with oblique top rods is designed. The inclined toprod is slid laterally in the corresponding slanting bar fixed plate. Under thethrust of the wear-resistant plate and the push plate, the rod not only movesupward, but also moves a segment of distance to its inclined direction, whichhas both the push and side pumping; the injection mold with the latent horngate is characterized by the automatic separation of the gate and the plasticparts; no other treatment of the gate position is needed; the gate will notproduce the gate on the surface of the plastic parts. The key to the design ofthe mold is to allocate the stroke of the inclined rod and the ejection of thestroke so that there is enough ejection to top out the product and use thenitriding treatment and quenching treatment to improve the performance of theparts.
Keywords: Automobile refueling cover plate; injection mould; inclined topmechanism; latent gate.
目 录
1 绪论................................................................... 11.1模具在现代化工业生产中的作用.............................................................................. 21.2中国塑料模具行业的现状.......................................................................................... 21.3模具行业在世界上的发展趋势.................................................................................. 31.4注塑模具设计、制造的特点...................................................................................... 31.5设计内容...................................................................................................................... 42 塑件的工艺性分析........................................................ 52.1 塑件相关结构工艺性分析......................................................................................... 52.2塑件原料(PPE)的成型特性和工艺参数..................................................................... 62.2.1 PPE塑料主要的性能指标.............................................................................. 72.2.2 PPE的注射成型工艺参数.............................................................................. 83 注塑设备的选择.......................................................... 93.1注射成型工艺过程...................................................................................................... 93.1.1模具需要塑料熔体注射量............................................................................... 93.1.2分型面上的投影面积及锁模力....................................................................... 93.2初选注射机.................................................................................................................. 93.3模架的选定................................................................................................................ 103.4 注射机的校核............................................................................................................ 113.4.1最大注射量校核.............................................................................................. 113.4.2 锁模力校核..................................................................................................... 113.4.3 模具与注射机安装部分相关尺寸校核........................................................ 124 型腔布局与分型面设计................................................... 134.1 型腔的布局............................................................................................................... 134.2 分型面的设计........................................................................................................... 135 注射模浇注系统的设计................................................... 145.1 主流道的设计........................................................................................................... 145.2 主流道衬套的设计................................................................................................... 145.3 分流道的设计........................................................................................................... 155.3.1分流道截面形状............................................................................................. 155.3.2分流道的尺寸确定......................................................................................... 155.3.3分流道的表面粗糙度..................................................................................... 165.4 浇口的选择............................................................................................................... 165.4.1 浇口的选用.................................................................................................... 165.4.2 浇口位置的选用............................................................................................ 175.4.3 浇注系统的平衡............................................................................................ 185.4.4冷料穴的设计................................................................................................. 185.4.5 排气的设计.................................................................................................... 186 模具成型零件的设计..................................................... 196.1模具成型零部件(型腔、型芯)的工作尺寸计算................................................ 196.1.1型腔相关尺寸计算......................................................................................... 206.1.2型芯相关尺寸计算......................................................................................... 216.2模具成型零件(型腔、型芯)的结构设计............................................................ 216.2.1 凹模结构设计................................................................................................ 216.2.2 型芯结构设计................................................................................................ 226.3模具成型型腔侧壁与底板厚的计算........................................................................ 226.3.1型腔侧壁计算................................................................................................. 226.3.2型腔底板厚度确定......................................................................................... 237 合模导向机构的设计..................................................... 247.1导柱结构.................................................................................................................... 247.2导套结构.................................................................................................................... 248 脱模机构的设计......................................................... 258.2 推杆设计................................................................................................................... 258.2.1 推杆的形状.................................................................................................... 258.2.2 推杆的位置和布局........................................................................................ 269 斜顶杆顶出机构......................................................... 279.1斜顶杆机构的工作原理............................................................................................ 279.2斜顶杆固定座............................................................................................................ 309.3斜顶杆定位块............................................................................................................ 3110 温度调节系统的设计.................................................... 3210.1温度控制系统的设计原则...................................................................................... 3210.2冷却管道的详细计算.............................................................................................. 3210.2.1 相关数据准备.............................................................................................. 3210.2.2计算凹模冷却回路有关参数....................................................................... 3310.2.3 计算型芯冷却回路有关参数...................................................................... 3510.3 模具加热系统的设计............................................................................................. 3511 模具的装配........................................................... 3611.1 模具的装配顺序与要点.......................................................................................... 3611.2 模具工作过程.......................................................................................................... 36结论..................................................................... 38致 谢.................................................................... 39参考文献................................................................. 40附 录.................................................................... 41附录A 英文原文............................................................................................................. 41附录B 中文翻译............................................................................................................. 591 绪论
本次毕业设计课题时来源于生活中比较常见的汽车加油盖板,它主要应用在汽车油箱处,主要为了遮蔽油箱,使汽车看起来更美观,加油盖板经历了从无到有,从金属材质到现在的高分子材质,模具生产出的加油盖板成型更加美观,产量和良品率都很高,同时使用上了高分子材料使重量更轻,产品表面美观,非常方便加工装配。并且材料还可以进行回收利用。同时并且兼顾防盗的作用;虽然加油盖板外形看似简单,但内部有许多卡扣部分较为复杂,另外它的加工工艺较高是一个难点?它的表面精度要求非常高,圆弧部分过渡完美,另外从侧面看是由直线和弧面交接而成,这给成型零件设计时提升了难度,并且还包括许多定位圆圈,为此查阅了大量相关资料,得出斜顶杆机构是解决卡扣的完美方式,斜顶机构可以侧向移动的同时向上顶出,兼具侧抽和顶杆的作用。在设计斜顶使要控制好抽芯距离,以免抽芯距过大撞坏型芯。同时为了使塑件成型更加美观,选择弧形浇口使浇口使浇口位置更加隐蔽,从而使其更加美观。同时由于塑件本身体积较大,使得模具必然体积很大,所以在设计型腔排布时需要注意。在设计冷却水道时要将型芯和型腔分开设计,型芯部分冷却要加强设计,因此需要进行冷却水道详细计算。使其充分散热从而塑件成型更加顺利。在大学期间经历了四次课程设计,有减速器设计、换热器设计、注塑模具设计、厂房设计。均得到了不小的收获。无论是在相关设计步骤上还是绘图软件的运用上都更加熟练,本次毕业设计的题目为奥迪汽车加油盖板的注塑工艺与模具设计。
本设计包括了汽车加油盖板的相关知识,且考验相关绘图软件二维和三维的运用能力,同时涉及工程制图相关知识,考察了我们对注塑模具相关知识的综合运用能力同时具有很好的检验效果?在设计汽车加油盖板模具的同时总结了以往注塑模具设计的一般方法步骤,并按照步骤依次设计,会用到以往常用的公式?图表?模具结构及模架相关参数和零部件?把以前学过的模具设计基础知识融入到本次加油盖板设计当中来?在设计中除使用传统方法外,同时引用了CAD(二维部分)?UG(三维塑件部分)等绘图软件,对二维制图和三维建模方面的运用有了更加深刻熟练的认识。同时使用Office办公软件按照要求进行格式的转换和修正,从而锻炼了我们的综合能力,为之后的工作和学习打下了基础。
1.1模具在现代化工业生产中的作用
模具在市场的应用十分广泛,并且它成本低,生产效率高;使得模具成为产品生产的主导者。模具的应用不仅在工业上、科技上还是生活中都有极大的应用前景。模具产业的不断发展,可以极大的推动我们生产的发展,能是我们用上做工优良而且价格实惠的产品。并且随着高科技和人工智能的不断进步,模具的科技含量肯定会越来越高,产品肯定也会越来越优质,从而推动人类的进步,提高人类的生活品质。使得模具在现代化生产的应用越来越受欢迎。
模具在汽车行业中生产了许多零件产品,例如保险杠,车内仪表盘及各种装饰,使汽车看起来更加一体化更加美观,从而修饰那些有危险或不美观的地方。汽车行业的发展离不开模具的推动。模具在电子行业的应用更为广泛,各种电子产品的外壳,其形状都是由模具来创造的,模具赋予电子产品更加多元化的外观,使电子产品更加复合消费者的要求。模具在家具中也得到广泛的应用,灯饰,窗帘轨道,各种管道都需要模具来成型。
1.2中国塑料模具行业的现状
虽然我国已经为模具生产大国与贸易大国,从数量和产量上已经超越许多工业发达的国家,但我国生产的模具在技术上与发达国家还有很大的差距。由于相关专业人士相对较少,虽然从事模具行业的人员很多,但真正的模具高级工程师在国内少之又少,总体缺乏经验,缺少勇于创新探索的能力。企业在模具方面的研发能力欠缺,整体技术落后于国际水平。
随着模具科技的发展,模具订购方对模具的质量要求越来越高,交货时期也越来越短中低档模具价格竞争激烈,中国的模具性价比优势不明显,这些客观诸多因素造成了模具企业生存发展难度加大。从而导致模具产业间竞争十分激烈。中国的模具厂商只有不断加大研发力度,增大生产能力,使得模具科技不断进步,力求达到国际水平甚至超越国际水平。成为世界上的佼佼者。
注塑模具制造的四大特点,及企业本身的综合能力,制约了模具企业的发展。摆在我们面前的主要问题是:理念、设计、技术、工艺、经验等方面总体仍然落后于国际水平。我国生产出的模具在工艺上,仍落后于发达国家,模具人才短缺,企业管理不够先进,信息化程度较低。
1.3模具行业在世界上的发展趋势
模具的生产在许多领域有着广泛的应用,例如军事、航天、汽车电子等;用模具生产出的产普具有成本低、高效等优点。模具生产的水平和科技含量决定产品的质量和公司的效益。这些已经成为一个国家科技与制造能力的的标志。决定着这些都体现了模具在国民经济中的重要地位。模具行业在世界上有非常优秀的发展前景,是现代工业的基础,在许多工业领域有着非常大的作用。
随着全球经济发展与科学技术的不断进步,从而导致各个国家在模具行业的竞争越来越激烈,各个企业不断升级自己的工艺水平,力求达到更加优质的模具产品。不断升级服务,达到最快的市场响应。不断更新自己的设计标准,并应用现代的信息技术加强管理,从而提升企业的综合能力。随着人工智能、纳米技术、3D打印的不断发展,模具可以更加快速的进行技术迭代,材料性能也会更加优秀。模具的制造也会更加方便。
如今的模具市场面临着各个国家之间的竞争。所以我们要加大创新力度,缩短生产周期,要求模具企业通过转型升级来适应市场全球化的环境,不断加大研发力度,大量招募模具人才,不断完善体系,引领世界的潮流,在世界模具行业里由重要的地位。zai让企业不但要做大还要做强。
塑料模具行业的发展趋势,提高模具标准化、通用化、数字化水平。在CAD/CAE/CAM一体化基础上建立三大数据库:模具标准、通用件的数据库,通用定型模具系列产品的数据库,以制品分类为基础的模型原型结构设计系列的产品数据库。
1.4注塑模具设计、制造的特点
模具产品特殊,它是单一产品,制造成本高;不同的模具结构差异很大,相同的模具几乎没有,这给工艺、设计、制造和管理带来困难。制造工艺复杂,加工动、定模的成型零件设备投资大。模具制造周期短:有的模具在签订合同前后花费了很长时间,一旦签订协议后,时间就会按日计算,交模时间紧迫。模具市场竞争激烈,同行间价格竞争、交模周期竞争、质量竞争等。模具一旦损坏维修成本较高。由于模具是由许多零件组合而成,精细度较高,考验工人的熟练度,使模具的管理维修带来困难。并且模具具有单一性,每一个模具的结构都有其不同,所以制造的时间短成本高,模具同行间竞争十分激烈。并且注塑模具的工作工程:由粒料放入料筒中加热熔融后加入注射机后经过保压冷却成型后,用顶杆或推件板推出,使塑件平稳推出。
1.5设计内容
对加油盖板的工艺性能和成形性能进行分析,针对各个倒角卡口难点部分进行详细分析,设计加油盖板的注塑工艺;初选注射机,选择对应的模架;对型腔进行合理布局和分型面的设计;对浇注系统进行设计;对成型零件进行分析计算;对导向机构进行设计选择;进行冷却计算;最后进行模具的装配。设计一套用于生产加油盖板的注射成型模具,按照注塑模具的设计步骤进行各部分详细计算。并用三维软件画出塑件三维图,用二维软件画出装配图和零件图。
2塑件的工艺性分析
2.1 塑件相关结构工艺性分析
图2.1 加油盖板CAD二维图
图2.2加油盖板UG三维图
2.2塑件原料(PPE)的成型特性和工艺参数
PPE聚苯醚是一种具有突出性力学性能和耐热型及优良介电性能和耐腐蚀性能优良的热塑性工程塑料,并且它耐水,耐水蒸气,无毒无污染,耐燃烧,而且尺寸稳定性好?其特点如下:
一般性能:PPE为非极性非结晶,低温为牛顿流体,高温为非牛顿流体型线性聚合物,其外观为琥珀色透明料,质地坚而韧,吸水性小,耐水,成型收缩率小,仅为0.7%~0.9%,可制作MT2级精度制品,注射塑料品的表面粗糙度可达到Ra=0.2
m。
力学性能:PPE中含有这大量的芳香环结构,分子链刚强,所以力学性能优良,主要表现在:强度高:尤其是在弯曲强度?拉伸强度?冲击强度较高,优于PA6?PC?PA66等塑料,其力学性能对温度和湿度的变化不敏感,在-135℃~150℃使用温度范围内,低温能保持韧性?高温也能保持强度和刚性?此外其分子结构中无极性和水解基团从而可以耐沸水和水蒸气?在沸水中加热700小时后,其拉伸强度?伸长率?抗冲击性几乎不变?抗蠕变性好 例如在23℃?21MPa的负载下,经3000h后蠕变值仅为0.75%,而此时PC的蠕变值已经达到1%,PA6的蠕变值大2.3%,ABS的蠕变值达到3%,所以PPE的抗蠕变型好,随着温度的提高PPE的蠕变值变化非常缓慢,具有很好的尺寸稳定性?刚性大,硬度高 其弹性木梁大于PC小于POM,但高温潮湿状态下耐磨性能尚可?抗疲劳及耐应力开裂性差 极端疲劳强度为8Mpa,但用增强PPO等塑料能提高疲劳强度?
热性能:PPE的热变形温度在1.82MPa下可达174℃,优于PA?PC?POM?ABS,与PF不饱和聚酯等热固性塑料相当,其脆化温度为-170℃,玻璃化温度为210℃,由-170℃到190℃,长期使用温度范围为-127℃到121℃,无负载间歇使用温度可达205℃?
PPE在空气中的热稳定性较好,熔点为267℃,热分解温度350℃,在热水?蒸汽中耐热性也很好,经过反复加热以及在150摄氏度的热空气加热150h,其性能几乎不变,但抗氧化性差,在氧气中加热到121℃就会起交联反应,到430℃左右可完全演变成热固性塑料?
PPE的线胀系数很小,有利于制作有嵌件及尺寸精度较高的制品;热导率中等,属于自熄,阻燃燃料,加入少量含磷阻燃剂即可达到阻燃级别,烟密度为538,燃烧时产生浓烟和腐蚀性气体?
电性能:PPE塑料结构中无强极性基团基因,属于非极性塑料,电性能稳定,介电性能优良,并且电性能受温度?湿度?频率变化影响较小?
耐化学药品性:PPE中无极大极性基团,玻璃化温度高,故耐水及耐热水性能优良,在热水中长期浸泡,其物理性能变化很小?
耐候性:PPE塑料在自然环境中,对热氧化(热老化)?湿气?臭氧氧化?燃烧生物老化的抵抗性较好,属于中等品级,但对于光氧化的作用抵抗性很差,长期在阳光或荧光照射下会吸收紫外线从而分解,所以需要加入防紫外线剂及抗热氧化剂?
环保安全性:PPO塑料无毒无害,污染性小,可做医疗?食品用制品,其大部分用作结构零件,便于回收,对环境影响较小,而且加工中只要没有发生热解或者热氧化,废料就可以100%回收利用,在日常生产中允许重复3次而不会降低性能?
2.2.1 PPE塑料主要的性能指标
表2.1 PPE塑料主要的性能指标
性能
温度
-17℃
23℃
93℃
密度/(g/cm3)
1.06
拉伸强度/MPa
80
55
断裂伸长率(%)
20-40
30-70
拉伸弹性模量/GPa
2.69
2.48
弯曲强度/MPa
134
114
87
弯曲弹性模量/GPa
2.65
2.59
2.48
蠕变性(300h,14MPa)(%)
0.5
悬臂梁缺口冲击强度/(J/m)
53(-40℃)
64
91
洛氏硬度(M)
78
疲劳极限(2x106次循环)/MPa
8
吸水率(%)
空气中,24h,50%RH
0.03
长期浸水
0.1
2.2.2PPE的注射成型工艺参数
表2.2 PPE的注射成型工艺参数
塑料
PPE
注射机类型
螺杆式
螺杆转速(r/min)
20~50
喷嘴
形式
直通式
温度/℃
220~240
机筒温度/℃
前段
230~250
中段
240~270
后段
230~240
模具温度/℃
60~80
注射压力/MPa
70~110
保压力/MPa
40~60
注射时间/s
0~5
保压时间/s
30~70
冷却时间/s
20~50
成型周期/s
60~130
3 注塑设备的选择
3.1注射成型工艺过程
3.1.1模具需要塑料熔体注射量
该 产 品 材 料 为 P P E , 查 文 献得 知 其 密 度 为 1 . 0 6 g / m 3 , 收 缩 率 为 0 . 5 % - 0 . 7 % [ 5 ] 。
由 U G 塑 件 三 维 图 得 出 一 幅 模 具 所 需 塑 料 的 体 积 :
V = 1 3 3 . 6 5 9 c m 3
质 量 M = ρ V = 1 . 0 6 X 1 3 3 . 6 5 9 = 1 4 1 . 6 7 9 g
总 注 射 量 : 1 . 6 m n = 1 . 6 × 1 4 1 . 6 7 9 × 2 = 4 5 3 . 4 4 g
3.1.2分型面上的投影面积及锁模力
通 过 计 算 加 油 盖 板 和 流 道 凝 料 在 分 型 面 上 的 投 影 面 积 : 有 公 式 3 . 1 得
A = n A 1 + A 2 ( 3 . 1 ) = 1 . 3 5 n A 1 = 2 × 2 2 . 1 × 1 4 . 4 × 1 . 3 5 = 8 5 9 . 2 4 8 c m 2
式 中 : A 1 — 单 个塑件 在 的 投 影 面 积 ;
A 2 — 流 道 凝 料 在 的 投 影 面 积
所 需 锁 模 力 , 由 公 式 3 . 2 :
F m= ( n A 1 + A 2 ) P 型 ( 3 . 2 ) = 8 5 9 . 2 4 8 × 3 5 = 3 0 0 7 . 3 6 8 K N
式 中 : P 型 — 塑 料 熔 体 对 型 腔 的 平 均 压 力 ( 本 设 计 取 3 5 M P a )
3.2初选注射机
根据塑料制品体积或质量及相关参数,查文献286~287可选定注塑机型号为XS-ZY—500[1]?
表3.1 XS-ZY-500参数
螺杆直径/mm
65
模具厚度/mm
最大
450
最小
300
注射容量/(cm3或g)
500
模板行程/mm
700
注射压力/105Pa
1040
喷嘴
球半径/mm
18
孔直径/mm
7.5
锁模力/10kN
350
定位孔直径/mm
150
最大注射面积/cm3
1000
推出
中心孔径
150
两侧
孔径/mm
24.5
孔距/mm
530
3.3模架的选定
由于塑件为大批量生产,故选择标准模架,选择A型模架;适用于本设计的薄壁型塑件。根据塑件选定模架为基本型A3,模板尺寸600×1000mm,编号为:
模架 A 60100-140×140×160GB/12555-2006 ,如图3.1所示:
图3.1 A型模架
模架相关参数具体见表3.2;
表3.2 模架参数
尺寸符号
单位(mm)
尺寸符号
单位(mm)
W
600
W5
312
L
1000
W6
498
W1
700
W7
480
W2
116
L1
952
W3
360
L2
880
A
140
L3
676
B
140
L4
868
C
160
L5
488
H1
60
L6
724
H2
90
L7
868
H3
60
D1
60
H4
90
D2
50
H5
40
M1
4xM60
H6
50
M2
4xM20
W4
256
3.4 注射机的校核
3.4.1最大注射量校核
注塑机的实际注塑量是注塑机的最大注塑量的80%,选用的注塑机最大注塑量应满足以下公式3.3:
0.8 V注射机 ≥ V塑件+V浇注系统 (3.3)
V机=500cm3 V塑=282cm3 V浇=85cm3
式中:V机——注塑机的最大注塑量 ;V塑——塑件的体积
V浇——浇注系统体积
故 V机=400≥367cm3
由于本设计选定的注塑机的注射容积为500cm3,符合要求?
3.4.2 锁模力校核
注射机的锁模力T合必须大于该模的推力当高压的塑料熔体,即
T合 ≥T推 (3.4)
T推=A×P平均≤A×k×P0=3118.1KN
T合=3500KN
式中:T合——注射机额定锁模力;
T推——型腔内塑料熔体沿轴向推力;
P平均——型腔的平均压力;
k——锁模力安全系数,一般取k0=0.2-0.4,本设计取0.3;
A——加油盖板与浇注系统在分型面上的投影面积;
P0——注射压力?
故T合 ≥T推;
所以本加油盖板设计选定的注塑机的压力满足要求?
3.4.3模具与注射机安装部分相关尺寸校核
(1)模具的厚度和外形尺寸的校核
已知:H m i n = 4 1 0 m m H m a x = 7 3 0 m m H = 5 9 0 m m
H m i n — — 注 塑 机 允 许 的 最 小 模 厚
H m a x — — 注 塑 机 允 许 最 大 模 厚
H — — 模 具 闭 合 高 度
故 满 足 H m a x > H > H m i n 要 求 ?
(2)开模行程的校核
由于本加油盖板的设计最大行程与模具厚度有关;故该情况开模行程应满足下式3.5:
已知:Smax=700mm; H1=24mm;H2=33mm
S机-(H模-Hmin)>H1+H2+(5~10) (3.5)
Smax———注塑机最大开模行程,
H1——顶出距离,
H2———塑件的厚度(其中包括浇注系统的凝料),
本设计由于为单分型面关系,且最大行程与模厚有关;
由于700>590+33+24+(5~10)
本设计开模行程满足条件?
4 型腔布局与分型面设计
4.1型腔的布局
在本设计中,塑件材质为PPE(聚苯醚),如果采用单型腔模具,塑件精度不高。按照制品的精度确定型腔数:生产经验认为,每增加一个型腔,塑件尺寸精度都会降低4%[2]。
考虑到模具成型零件和抽芯结构以及浇口位置和出模方式的设计,本设计设定型腔数目为2;模具的型腔排列方式如图4.1所示:
图4.1型腔布局
4.2分型面的设计
根据本设计中加油盖板的外观特点,本设计选用塑件的最大平面平分处为分型面,开模后塑件留在动模一侧,分型面如图4.2所示:
图4.2 加油盖板的分型面
5 注射模浇注系统的设计
5.1主流道的设计
主流道的一端与注射机喷嘴相接触,可以看作是喷嘴的通道在模具中的延续,另一端与分流道相连的一段带有锥度的流动的通道?
本设计采用了潜伏式弧形浇口,为方便拉出流道中的凝料,将主流道部分设计为锥形,角度为3°;内表面粗糙度为Ra=0.4
,主流道大端为圆角,取r=2mm,H=12mm,r1=30mm,r2=30+2=32mm;
图5.1 主流道
5.2 主流道衬套的设计
本加油盖板设计将主流道部分设计为主流道衬套,并且T10A碳素钢单独加工和热处理,其大端兼做定位圈,圆盘突出定模端面部分长的H=5~12mm;本设计取H=12mm?由于加油盖板材质为PPE,需要在主流道处采用电加热提高料温?如图5.2所示:
图5.2 主流道衬套
5.3分流道的设计
在分流道的设计中应考虑尽可能避免熔体温度降低和尽量减小在流道内的压力损失,同时还要减小体积[1]?
5.3.1分流道截面形状
:本设计分流道截面形状为圆形截面,从而实现效率最大化?
5.3.2分流道的尺寸确定
(5.3)
式中 :D―分流道直径(mm)
m―塑件的重量(g)
L―分流道的长度(mm)
表5.1 部分分流道直径范围
塑料品种
分流道直径/mm
塑料品种
分流道直径/mm
ABS?AS
聚甲醛
丙烯酸酯
耐冲击丙烯酸酯
尼龙-6
聚碳酸酯
4.8-9.5
3.2-9.5
8.0-9.5
8.0-12.7
1.6-9.5
4.8-9.5
聚丙烯
聚乙烯
聚苯醚
聚苯乙烯
聚氯乙烯
4.8-9.5
1.6-9.5
6.4-9.5
3.2-9.5
3.2-9.5
由表5.1中可知,聚苯醚的分流道直径在6.4~9.5之间,本设计取8mm?
图5.2分流道截面
5.3.3分流道的表面粗糙度
分流道的表面粗糙度通常取Ra=1.25~2.5
,这可以使外层塑料冷却皮层固定,增加对外层塑料熔体流动阻力,形成绝热层,有利于保温[2]?
本加油盖板设计取Ra=1.5
5.4浇口的选择
5.4.1浇口的选用
:本设计的浇口采用带有直流道与分流道的潜伏弧形浇口,又称为羊角浇口,如图5.3所示:
图5.3 潜伏弧形浇口
优 点 : 浇 口 在 成 形 时 可 以 自 动 切 断 , 从 而 有 利 于 自 动 成 形 。 浇 口 的 痕 迹 不 明 显 , 通 常 不 需 要 后 加 工 ?
缺 点 : 浇 口 压 力 损 失 比 较 大 , 必 须 提 高 之 射 出 压 力 ; 设 计 并 不 合 理 浇 口 凝 料 容 易 折 断 而 堵 塞 交 口 ? 在 注 射 过 程 中 可 能 在 表 面 出 现 烘 印 ?
本设计中采用的潜伏式弧形浇口相关数据如下:D=8mm,A=13mm,底边圆角为0.8d=4.8mm,浇口与塑件接触位置d=1mm,其他参数见图5.4
图5.4 潜伏弧形浇口参数
5.4.2浇口位置的选用
浇口的位置和尺寸要求非常严格,要使塑件的外表性能良好,一定要认真考虑其位置,通常要考虑以下几项原则:
浇口位置应使流程最短,料流变向最少,防止型芯变形?
浇口位置和数量应有利于减少熔接痕和增加熔接强度?
浇口位置应考虑取向作用对性能的影响?
浇口处应避免弯曲和受冲击载荷?
尽量开在不影响塑件外观的部位?
注意对外观质量的影响?
在本设计中,浇口位置选择在加油盖板水平面下方?如图5.4所示;
图5.4浇口位置
5.4.3浇注系统的平衡
本加油盖板设计由于采用的是平衡式浇注系统。其特点:从分流道到浇口及型腔,其形状?圆角半径?模壁的冷却条件、长宽尺寸等都完全相同[2]。从而获得尺寸相同?物理性能良好的塑件?
显然,本次加油盖板模具设计的一模两腔是平衡的,即从主流道到各个型腔的分流道的长度分别相等,截面尺寸及形状都相同?
5.4.4冷料穴的设计
本 设 计 的 直 径 取 为 6 m m , 要 保 证 冷 料 体 积 小 于 冷 料 穴 体 积 ? 冷 料 穴 的 倒 扣 形 式 有 很 多 种 ( Z 字 形 、 倒 锥 形 等 ) ,
本 设 计 采 用 倒 锥 形 的 冷 料 穴 ; 它 与 推 杆 配 合 使 用 , 开 模 时 倒 锥 形 的 冷 料 穴 先 将 主 流 道 凝 料 拉 出 定 模 , 最 后 在 推 板 和 斜 顶 杆 的 作 用 下 将 冷 料 和 主 流 道 凝 料 随 制 品 一 起 被 顶 出 动 模 ? 如 图 5 . 5 所 示 :
~
图5.5 倒锥形冷料穴
5.4.5排气的设计
设置排气槽可降低注射压力,是塑件更容易成型,可以提高生产效率降低生产成本从而降低消耗。
排气方式:用分型面排气;用顶杆运动间隙排气;用型芯与模板配合间隙排气;用侧型芯运动间隙排气;开设排气槽?
本设计利用模具零部件的配合间隙及分型面自然排气?
6模具成型零件的设计
模具成型零件尺寸必须保证成型零件的尺寸达到要求,然而影响塑件尺寸及公差的因素相当复杂。影响成型零件的因素包括以下几点:
成型零件的制造公差直接影响塑件的制造公差[2]。确定成型尺寸前应该首先搞清楚各部分尺寸的性质分类以便确定各部分尺寸及其公差的取向。
成型零件的尺寸计算要考虑成型收缩率的波动因素,其中包括:塑件的生产工艺条件、模具结构、操作方式、材料等。
注意塑料制品的厚度控制,一般宜薄不宜厚;注意修正值的控制:动模适当做正值,定模适当做负值,便于调整尺寸。
成型零件的尺寸标注要考虑制品的装配要求,便于试模后的修整。
动定模的镶芯零件的装配尺寸根据配合公差表正确使用,从而便于零件化生产和模具的日常维护。成型零件的尺寸设计在模具中十分重要,所以才设计使必须要保证成型尺寸达到要求。
6.1模具成型零部件(型腔、型芯)的工作尺寸计算
图6.1 塑件侧面结构
根据塑件尺寸查表GB/T14486-93公差数值标准表得:
表6.1 塑件尺寸公差表
尺寸符号
数值/mm
公差值
D1
D2
D3
H1
H2
d1
d2
d3
h1
h2
70
14
60
35
7
70
14
60
30
23
±0.53
±0.29
±0.42
±0.38
±0.24
±0.53
±0.29
±0.42
±0.38
±0.34
6.1.1型腔相关尺寸计算
(1)型腔长度类尺寸
(6.1)
式中: Lm — — 定 模 尺 寸 ; 单 位 为 m m
— — 平 均 收 缩 率 ;
— — 塑 件 的 基 本 尺 寸 ; 单 位 为 m m
— — 塑 件 的 公 差 值 , 塑 件 按 M T 3 查 取 ;
— — 模 具 成 形 零 件 的 制 造 公 差 ; 取 / 4
代入表格中数据;
=70mm,LM=70.75
=14mm, LM=13.85
=60mm, LM=59.99
(2)型腔深度尺寸
=[(1+Scp%)
-
Δ]
(6.2)
式中:
----型腔深度尺寸;单位为mm
----塑件的基本尺寸;单位为mm
代入数据得:
=35mm, HM=35.43
=7mm, HM=7.2
6.1.2型芯相关尺寸计算
(1)型芯的径向尺寸计算
(6.3)
式中:
——动模尺寸;单位为㎜
——平均收缩率;
——塑件的基本尺寸;单位为㎜
——塑件的公差值,塑件按MT3查取;
——模具成形零件的制造公差;取
/4
=70mm,lM=70.75
=14mm, lM=13.85
=60mm, lM=59.99
(2)型芯高度尺寸计算:
=[(1+
)
-
Δ]
(6.4)
式中:
----型芯高度尺寸;单位为mm
----塑件的基本尺寸;单位为mm
=30mm,
M =29.90
=23mm,
M =22.90
6.2模具成型零件(型腔、型芯)的结构设计
6.2.1 凹模结构设计
本设计模具采用整体嵌入式凹模,采用侧壁定位螺钉方式固定,采用一模两腔的形式。
由于其表面较复杂,在很难对其进行具体的测量和计算,因而在设计模具型腔时,根据PPE塑料的收缩率,采用MT5级精度进行加工,表面粗糙度为Ra0.4?本设计凹模结构如图6.2所示:
图6.2 凹模结构图
6.2.2型芯结构设计
□□本设计型芯结构为整体嵌入式,采用螺钉连接;如图6-2所示?
图6.3型芯结构图
6.3模具成型型腔侧壁与底板厚的计算
6.3.1型腔侧壁计算
由于本加油盖板设计型腔为整体式矩形型腔;在塑料熔体压力作用下,其最大变形在自由边的中点,变形量为:
(6.5)
C值在表取0.084,由于本设计l=221mm,所以按允许变形量[
]=0.05mm,计算壁厚;
按刚度条件,侧壁厚度为:
(6.6)
=8.435
6.3.2型腔底板厚度确定
本设计为整体式矩形型腔底板,可以视为周边固定受均分布的载荷的矩形板,在塑料熔体压力P的作用下,板的中心产生了最大变形,为:
(6.7)
C’在表中可以查到,C’=0.024;按刚度条件计算底板厚度;
(6.8)
=36.628
7 合模导向机构的设计
为使开模合模时使动定模能够准确对合,从而设计导柱导套结构,在设计时必须导向精确,定位精准。有足够的强度,刚度和耐磨性。
7.1导柱结构
带头A型导柱如图7.1所示:材料T10A,D=60mm,S=20mm,d=44mm,L1=80mm,L=239mm。
图7.1导柱
7.2导套结构
带头台肩式导套如图7.2所示:材料T10A;D=44mm,d1=64mm,d2=84mm,L1=80mm,H=20mm,R=3mm。
图7.2导套
8 脱模机构的设计
推出机构应结构简单,动作可靠,开模时应使塑件留在动模,从而利于注射剂锁模装置的顶杆或液压缸的活塞推出塑件。保证准确灵活;不留推出痕迹。运动准确灵活,本身要有足够的强度。推出位置选择塑件隐蔽处使外表面不留痕迹,使塑件更加美观完整,使塑件能够完整顺利的脱模。
8.2推杆设计
本设计只需用推杆端面参与,由于推杆直径较小,并且不与要顶出较大的距离,采用单节式推杆?
推杆和推杆孔配合为H8/f8,Ra=0.8um;且采用最常用的推杆固定形式,固定孔直径d1=d+0.75mm=14.75mm。
8.2.1 推杆的形状
□□
如图8-1所示:
图 8.1 推杆
8.2.2推杆的位置和布局
本设计的推杆只作为拉料杆使用,位置在弧形浇口的中心处。
图8.2 倒锥形拉料杆
9 斜顶杆顶出机构
斜顶杆设计的顺序如下:
根据实际行程确定斜顶杆的角度,斜顶杆的角度一般为:3°,5°,8°,12°。
根据勾位的宽度确定斜顶杆的宽度?
根据斜顶杆的宽度确定斜顶杆固定座的形式?
根据斜顶杆的长度和宽度来确定耐磨快的长和宽,耐磨块的厚度一般取15mm,其材质为:2510?
在设计斜顶杆时一定要算清斜顶杆的行程和顶出的行程,以便有足够的顶出量来顶出产品,通常斜顶杆的顶出余量比实际大0.5~2mm?
通常斜顶杆材质为8407,且要淬火到48-52HRC,普通的斜顶用718H氧化?斜顶杆固定座常采用T槽形式,但在斜顶杆很薄的情况下,常采用固定座形式,固定座采用WY718,且都需要表面氮化处理?
9.1斜顶杆机构的工作原理
斜顶杆在对应的斜顶杆固定板中侧向滑动,斜顶杆与斜顶杆耐磨板配合?靠推板从下而上给斜顶杆一个推力推动斜顶杆向上的推力。起到既有推出又有侧抽作用,设计要点如9.1所示:
图9.1斜顶杆结构
设计要求:其中:S≥A+(2-3);B>S;3°≤C≤15°,D≥6,G≥3-5,H≥S+(2-3),I≥4,J≥3.
:由于本设计有三种不同的卡扣,共七个卡扣;所以设计三种斜顶杆,如下图9.2,9.3,9.4?
图9.2斜顶杆A
图9.3斜顶杆B
图9.4斜顶杆C
9.2斜顶杆固定座
斜顶杆固定座与斜顶杆配合使用,斜顶杆通过斜顶杆固定座中间的T形槽滑动且与斜顶杆定位块配合?
图9.5 非标准型斜顶杆固定座
本设计由于斜顶杆较大,选择非标准型固定座?T=20,W1=30,L=60,W=50,H=50,如图9.6所示;
图9.6 斜顶杆固定座
9.3斜顶杆定位块
由于本设计塑件尺寸较大,采用非标准型定位块?如图9.7所示;
图9.7斜顶杆定位块
10温度调节系统的设计
模具温度低,熔融塑料固化时间短,成型周期相应也短,但塑料流动性较差,可能会出现型腔充填不满的现象。模温控制系统设计的好,可缩短冷却时间,提高塑件质量;反之,如果模温控制机构不合理,会延长塑件成型周期,甚至塑件会变形。所以为了保证塑件能够平稳顺利的出模,要进行相应的温度调节设计。
10. 1温度控制系统的设计原则
温度均衡原则:模具中不能出现局部过热过冷的现象。要控制水道进出口的流量压力降、温度差。动、定模冷却回路应分开设计。
区别对待原则:模具的温度根据使用的塑料的性能使用。动模型芯必须重点冷却。
含有蚀纹的型腔、留花火纹的型腔,其定模温度应比一般抛光面要求的定模温度高。
冷却水道设计为防止温度下降熔接痕会更严重,应避免设置在制品熔接的部位。制品的冷却时间与塑料制品的尺寸壁厚塑料性能等都有关,主要取决于冷却系统的设计。
方便加工:冷却水道的截面积不可大幅度变化。直通式水道长度不可太长,应考虑标准钻头的长度能否满足加工要求。尽可能使用直通水道实现冷却循环。进出水管接头应设置在非操作侧或模具下方。总之,要做到优质?高效率生产,模具必须进行温度调节?
汽 车 加 油 盖 板 设 计 使 用 的 塑 料 是 P P E , 要 求 模 温 较 高 , 若 模 具 温 度 过 低 , 会 影 响 塑 料 的 流 动 性 , 增 加 剪 切 阻 力 , 使 塑 件 的 内 应 力 较 大 , 甚 至 还 出 现 许多缺 陷 ? 因 此 在 注 射 开 始 时 , 为 防 止 填 充 不 足 , 充 入 温 水 或 者 模 具 加 热 ?
本设计由于为大型模具,需要进行冷却管道详细计算。
10.2冷却管道的详细计算
10.2.1 相关数据准备
(1)数据准备
塑件材质为PPE,制件厚度为3mm,塑件质量为141.679g,加上流道凝料消耗,故一次注射量G=0.45Kg?查得PPE的单位热流量为590KJ/Kg.
设注射时间为t1=5s,冷却时间t2=30s,开模取件时间为7s,得注射周期=42s.由此得每小时注射次数N=3600/42=85次
将以上数据带入式(10-1)中得单位时间内型腔总热量;
Q=WQ1=NGQ1=85×0.45×590=22567.5KJ/h
由于本设计模具四侧面积Am1=2.08m2,Am2=0.6m2,开模率ηh为;
ηh=
(10-2)
=[42-(5+30)]/42=0.17
故散热表面积为AM=Am1+ηhAm2 (10-3)
=2.08+0.17×0.6=2.182
设模具平均温度:θ2m=60℃,室温θ0=20℃,据(10-4),对流散发热量Qc为:
(10-4)
=1562.24KJ/h
根据式(10-5),辐射所散发的热量QR为:
(10-5)
=106.57KJ/h
根据式(10-6)注射机工作台所传递的热量QL为:
(10-6)
=12048KJ/h
根据式(10-7),应由冷却系统从模具中带走的热量Q2为:
=Q-(QC+
+
) (10-7)
=27567.5-(1562.4+106.59+12048)=8850.69
应分别由凹模和型芯的冷却回路带走,采用式(10-8)的分配方案;
=0.4
=3540.28
=0.6
=5310.4
10.2.2计算凹模冷却回路有关参数
(1)制件与型腔壁温度差的平均值?据式(10-9),得:
(θ1-θ3)MG (10-9)
=
=
=86℃
设θ1max=230℃ θ3max=70℃ θ3min=50℃则
70℃,
由(θ1-θ3)MG=86℃,θ1max-θ3min=150℃,查图表得θ1min-θ3max=40℃,θ1min=120℃;
(2)凹模所需冷却管直径 设: θ5in=20℃, θ5out=23℃,则θ5M=21.5℃,
根据(10-10)有:
(10-10)
=11.76×10-3
由qv查表得水管直径D=20mm,冷却水直径最低流速v=0.66m/s
(3)热阻计算
用式
(10-11)
=5.63×10-4
(4)冷却水管壁的平均温度?
由式
(10-12)
=61.13℃
(5)凹模冷却水管回路总传热面积
由式
(10-13)
=0.0198m2
(6)凹模所需冷却水管的长度
由式
(10-14)
=0.316
根据凹模零件图实际总长对比,完全满足要求?
(7)雷诺数Re值的校核
当
=20.5℃时,查得水的运动黏度
=1.0×10-6m2/s,已知v=0.66m2/s,d=0.02m,根据式10-15:
(10-15)
=13200>104
故水的流动属于稳定湍流,有良好的冷却效果?
(8)冷却回路压降计算?
由图可知,凹模的冷却回路由8处90°转弯,得
=
=7.2m,再将其他已知数据代入(10-16)
(10-16)
=396.4Pa
该压力小于一般自来水压力,故该方案可靠?
10.2.3 计算型芯冷却回路有关参数
(1)制件与型芯壁温度差的平均值?据式(10-9),得:
(θ1-θ3)MG (10-9)
=
=
=129℃
设θ1max=230℃θ3max=80℃ θ3min=60℃ 则
70℃,
由(θ1-θ3)MG=129℃,θ1max-θ3min=150℃,查图表得θ1min-θ3max=40℃,
θ1min=120℃;
由于本设计分型面对称,凹模和型芯其余参数相同?
10.3 模具加热系统的设计
由于聚苯醚的熔融温度为200℃,并且流动性能较差,在注塑模具模温要求60~80℃;故本设计模具必须加热。模具的加热方法有电加热、水加热、油加热等。本设计采用电加热。
11 模具的装配
根据装配图和相关技术要求,将加工好的模具零部件和标准件,按照一定的工艺顺序和技术要求进行定位配合?紧固连接,从而达到生产要求,称为模具的装配[3]?对模具之间连接组合,达到生产的要求。
塑件的质量取决于模具的质量,只有模具结构合理,才能保证生产的塑件合理。模具必须保证有足够的寿命和性能。严格的说,经过了一段时间试生产出的制品合格后,未发现有精度和质量问题,才称的上合格的模具?
11.1模具的装配顺序与要点
确定装配基准;装配型芯?镶件要根据具体情况修磨,使配合间隙达标?对动?定模分别组装?然后进行配模,保证分型面的装配精度?装配导向系统保证开模合模动作灵活,无晃动和阻滞现象?调配好定模热流道系统,不流延?不堵塞?不漏电,阀门动作灵活?抽芯机构?斜顶要求滑动自如,调整好固定压板需要定位销定位?在装配顶出系统时,对多顶杆的顶出系统要调整好其复位和顶出装置?装配冷却或加热系统?保证管路畅通,不漏电?不漏水,阀门动作灵活?装配好液压气动系统,各管路应该连接紧密?牢固不得有任何泄漏;紧固所有连接螺钉?标准件不能随意改变尺寸?组装液压或气动系统,保证运行正常?总模具装配好后,对照图样检查所有配件,不能遗漏?由于模具零件较多,装配较为复杂,需要有专业的人士才能进行,每个模具的结构都不尽相同,所以模具设计较为昂贵。
11.2模具工作过程
11.1模具装配图
特点:该模具采用一模两腔,并通过设置斜顶机构和潜伏式弧形浇口,配以高效的冷却系统,时模具冷却比较均匀。由斜顶机构推出动作完成制品的脱模过程。
工作原理:充型冷却结束后,动模板(5)在动模固定板(1)带动下后退实现开模,然后推板(2)在注射机推杆的作用下,推动斜顶杆A(2)?斜顶杆B(25)及斜顶杆C(27)顶出塑件实现脱模,同时拉料杆拉断浇口,从而完成脱模抽芯动作?在合模过程中,通过复位杆和弹簧使斜顶杆复位,准备下次注射?
结论
本文主要介绍了关于奥迪汽车加油盖板的设计过程以及汽车加油盖板相关领域的发展历程,从金属材质到有机高分子材质,从主机厂商散件装配到整体模块化出模的历程,各种新材料?新技术不断在行业中涌现;目前我国已经采用上模块化加油盖板技术;随着技术的不断发展,汽车加油盖板有可能变为其他能源的盖板(混合动力,纯电动汽车等),甚至被其他产品取代?
在模具设计过程中,首先对产品进行了塑件分析,包括加油盖板的工艺参数,材质的工艺特性以及成型性质,对主要性能指标和成型工艺参数进行了解;然后计算注射量?锁模力,初选注射机;对开模行程?最大注射量进行校核;满足条件后对型腔进行布局(一模两腔),和对分型面的位置进行确定;然后进行浇注系统设计(主流道?分流道?浇口?冷料穴、排气),本设计加油盖板难点在于浇口位置在盖板下方一侧,需要设置潜伏浇口中的弧形浇口来设定才能满足要求,并且采用圆形截面分流道,从而保证外形没有明显浇口痕迹,排气结构采用分型面间隙排气。
在进行成型零部件结构尺寸计算时,首先对型腔的径向尺寸进行计算,通过分析本加油盖板设计采用整体式型腔。包括型腔的长度类尺寸和深度尺寸;其次对型芯的径向尺寸和高度尺寸计算?并且还有型腔侧壁及地板厚度的计算?第七章针对合模导向机构(导柱导套)进行设计,本设计采用A型导柱和台肩式导套;设计脱模机构时本设计由于有斜顶杆参与,只设计了拉料杆用于拉出凝料。
由于加油盖板的底部有七个卡扣式设计,所以需要进行斜顶机构方面设计,本设计采用了一体式斜顶杆,由于塑件存在三处结构不同的卡扣,所以设计了三种斜顶杆,其中两个为对称设计,另一个垂直于前两者,斜顶杆?导滑槽?固定座都需要进行氮化处理;在设计温度调节系统时,由于本设计为大型模具,需要进行冷却详细计算,包括冷却系统从模具带走的的热量量?注射机工作台的传递热量?对流散发热量等,从而确定冷却水管直径和所需冷却水管长度同时得保证水流动为稳定的湍流;冷却回路压力要小于一般自来水压力,模具装配时要充分了解装配顺序,以及开模的过程?如何复位,从而准备下次注射?同时完成装配图和相关零件图的绘制。
在设计过程中,设计了装配图和相关零件图,期间需要不断提高对软件的熟练度,并且充分了解汽车加油盖板的发展历程和技术迭代;通过这次的设计,使我对注塑模具设计有了更加细致化的了解,设计思路和方法有了更加深入的认识。
致 谢
本次汽车加油盖板设计是在周金华老师的细心指导下完成的,在设计的几个月中,从无法着手到一步步慢慢完成整个设计,老师一丝不苟的严谨教学态度让我们记忆深刻,在刚接触到塑件时,以为设计会比较简单,其中的卡扣部分起初以为只是需要侧抽芯就可以完成,后来开始着手设计时才发现自己过于天真。本设计一共有七个卡扣,其中六个互相对称,在两条平行的直线上,如果采用侧抽芯,会撞坏其中的卡扣导致设计失败,为此特意请教了周金华老师,经过相关的指导后,并查阅了相关书籍,得出斜顶结构可以完美解决卡扣问题。再有就是浇口位置的选择上必须保证浇口能使塑件顺利成型,经过老师指导和查阅大量书籍后得出潜伏式弧形浇口符合本设计要求。由于聚苯醚的流动性不太好,设计时与要进行冷却管道详细计算。在设计过程中周老师给了我们许多模具方面的建议和论文格式方面的建议。同时在设计工程中给予我们很大的鼓励和支持,之所以能够顺利的完成这次加油盖板的注塑模具设计是与老师的悉心指导分不开的,在论文完成之际,向周金华老师表示衷心的感谢和崇高的敬意!
在本次设计中,累积的经验来自于这四年课程设计的经验积累,这是与高分子专业老师们的教导是分不开的。只有在不断练习不断积累经验才能在这次成功完成这次毕业设计,本人还得到高分子材料老师的热心帮助,在此表示由衷的感谢!
参考文献
[1] 黄虹. 塑料成型加工与模具. 北京化学工业出版社. 2008:143~169,213~225
[2] 刘朝福.注塑模具设计师速查手册.北京工业出版社.2010: 309~310
[3] 石世桃.注塑模具设计与制造教程.化学工业出版社.2017:243~247
[4] 刘朝福.注塑模具典型结构图册与动画演示.化学工业出版社.2011:35~39
[5] 卓昌明.塑料应用技术手册.机械工业出版社.2012:380~386
[6] 马之庚, 陈开来.工程塑料手册.机械工业出版社.2004:135~139
[7] 杨裕根,诸世敏. 现代工程图学.北京邮电大学出版社. 2008:231~247
[8] 唐颂超. 高分子材料成型加工. 中国轻工业出版社. 2016:229~245
[9] 丁浩. 高分子材料成型加工基础. 中国轻工业出版社. 1982:89~96
[10] 徐佩弦.塑料制品与模具设计.中国轻工业出版社.2001:135~167
[11] 赵德仁,张慰盛.高聚物合成工艺学.化学工业出版社.2016:269~271
[12] 左演声,陈文哲,梁伟.材料现代分析方法.北京工业大学出版社.2016:35~39
[13] 唐志玉.大型模具设计技术原理与应用.化学工业出版社.2004:121~127
[14] 黄锐.塑料工程手册.机械工业出版社.2000:138~149
[15] 赵素和. 聚合物加工工程. 中国轻工业出版社. 2001:67~72
附 录
附录A 英文原文
Design andAnalysis of Plastic Injection Mould for CAM BUSH with Submarine Gate
A.1. Introduction
Now a day’s plastic are occupying a vitalrole in the day-to-day life. It is not at all can exaggeration, if we say thatthere is no field into which plastic have not stepped in right from themanufacturing at a pin to that of a spacecraft. At the middle of 19th century,plastics start a leading role in the material and in our life.Corrosionresistance are some of the aspects through which plastics are even becomingsuperiors to metals and attained an elevated rate of preference in every branchof manufacturing. Right from the emergency of plastics they are undergoingdrastic in various aspects like design of plastic product, manufacturingprocessing then in testing fields and now, because of fruitful efforts of manypeople at last the came in work through manual labor, but with help ofartificial intelligence that is, with software package like CAD/CAM. Because ofhigh strength of weight ratio, improve chemical and temperature resistance,inherent properties of being bath thermal and corrosion resistance,transparency have made them a material choice. Plastic consume less energyduring formation and can be profitably recycled. Today plastics are replacingthe metals like Brass, Copper, Cast Iron, Steel etc. Plastics can be classifiedaccording to manufacturing methods in to main groups Those which soften whenheated and solidifies on cooling. These are known as “Thermo plastic” and Those which harden whenheated as a result of chemical change. These are known as Thermosetting or Duroplastic material”Selection of particular material for the product is another important factor.This is particularly very necessary for the product determination. It shouldcapable of withstanding stresses acted upon it as well. Each material has itsown properties and attributes. Some materials are better in high environmentand extremely abrasion resistance. The difficult part is to find a materialthat will come close to fulfilling the entire requirement of the purpose. Somaterial should be so versatile that it suits all the consideration andrequirement of our product. After considering all these point’s material must be selectedsuitable enough to satisfy all these conditions.
A.2. Plastic Cam Bush for Transformer
The objective ofthe paper is to design and Analysis the injection mould tool for a cam bush ofan High voltage transformer. Cam Bush is used as a indexing device in ON/OFFLoad Tap changer device of high voltage transformer and serves as the connectorbetween the indexing head and the power changing gears. The indexing head isconnected to the gear by means of the shaft which is attached with the CamBush. The cam bush has two tail ends, one side is press fitted to the indexingcrank circle and the other side is fitted to the driving mechanism. Each holehas different driving mechanism, when the indexing circle rotates and the crankpin engaged in the first hole the first driving mechanism turns on. Thedifferent type of power is obtained by means of changing the index position.Cam bush serves as the connector between crank circle and the gears. It isprovided in the power changing indexing mechanism. The indexing crank circlehas many indexing holes, but the mechanism has 6 drive, so the cam bush with 6holes is provided in between the crank circle, speed indicator wheel and theshaft which is intersected in center and connected to the gears. This CAM BUSHis generally made with Polystyrene, Nylon6 and PVC. Due to high voltageregulating application this Cam Bush becomes heated up and wear off. Due torepeatedly applying pressure by regulating it, it becomes damage.
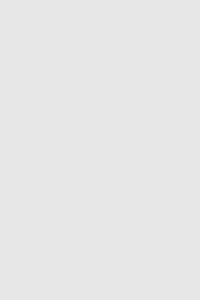
Picture A.1 Cam bush Solid Model and Assembly
Plastics are man-made materials. They areless brittle than glass, yet they can be made equally transparent and smooth.They are light weight and at the same time possess good strength and rigidity.They resist corrosion and the action of chemicals. They can be easily molded todifferent shapes. Commonly used thermoplastic materials are Polystyrene, Nylon6, P.V.C , Polypropylene etc. Mould making is an important role in plasticsindustries because the related products constitute more than 70% of thecomponents in consumer products. Injection moulding is a complex but highlyefficient means of producing a large variety of thermoplastic products and hasmany advantages, such as short production cycles, excellent surfaces of theproducts, and has no secondary operations, good results in moulding ofcomplicated shapes. The design and fabrication of injection moulding tool forcomplex plastic products is play a wider role to meet the industrial demandespecially in plastic industries. Hence, there is a demand in the industry forplastic injection moulding techniques capable of producing plastic parts.Literature review reveals that there is a lack of research on design andmanufacturing of injection moulding tool for complicated plastic components.Hence, this project focused on design and Analysis of Injection moulding toolwith baffle type cooling channel and submarine gate for cam bush.
A.3. Injection Moulding Process
It is amanufacturing process for producing parts by injecting liquid molten materialinto a mould. Injection moulding can be performed with a host of materials,including Metals, Glasses, Elastomers, Confections and most commonlyThermoplastic and Thermosetting polymers. Material for the part is fed into aheated barrel, mixed, and forced into a mould cavity where it cools and hardensto the configuration of the cavity. After a product is designed, usually by anindustrial designer or an engineer, moulds are made by a mould maker (ortoolmaker) from metal, usually either steel or aluminum, and precision-machinedto form the features of the desired part. Injection moulding is widely used formanufacturing a variety of parts, from the smallest components to entire bodypanels of cars. The part, the desired shape and features of the part, thematerial of the mould, and the properties of the moulding machine must all betaken into account. The versatility of injection moulding is facilitated bythis breadth of design considerations and possibilities Injection moldingutilizes a ram or screw-type plunger to force molten plastic material into amold cavity; this solidifies into a shape t
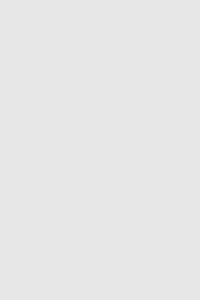
hat has conformed to the contour of the mold. It is most commonlyused to process both thermoplastic and thermosetting polymers, with the formerbeing considerably more prolific in terms of annual material volumes processed.
Picture A.2: Model of Injection Moulding Process
Injection molding consists of high pressureinjection of the raw material into a mold which shapes the polymer into thedesired shape. Molds can be of a single cavity or multiple cavities. Inmultiple cavity molds, each cavity can be identical and form the same parts orcan be unique and form multiple different geometries during a single cycle.Molds are generally made from tool steels, but stainless and aluminum molds aresuitable for certain applications. Aluminum molds typically are ill-suited forhigh volume production or parts with narrow dimensional tolerances, as theyhave inferior mechanical properties and are more prone to wear, damage, anddeformation during the injection and clamping cycles; but are cost-effective inlow-volume applications as mold fabrication costs and time are considerablyreduced. Many steel molds are designed to process well over a million partsduring their lifetime and can cost hundreds of thousands of dollars tofabricate. When thermoplastics are molded, typically pelletized raw material isfed through a hopper into a heated barrel with a reciprocating screw. Uponentrance to the barrel the thermal energy increases and the Vander Waals forcesthat resist relative flow of individual chains are weakened as a result ofincreased space between molecules at higher thermal energy states. This reducesits viscosity, which enables the polymer to flow with the driving force of theinjection unit. The screw delivers the raw material forward, mixes andhomogenizes the thermal and viscous distributions of the polymer, and reducesthe required heating time by mechanically shearing the material and adding asignificant amount of frictional heating to the polymer. The material feedsforward through a check valve and collects at the front of the screw into avolume known as a shot. Shot is the volume of material which is used to fillthe mold cavity, compensate for shrinkage, and provide a cushion (approximately10% of the total shot volume which remains in the barrel and prevents the screwfrom bottoming out) to transfer pressure from the screw to the mold cavity.When enough material has gathered, the material is forced at high pressure andvelocity into the part forming cavity. To prevent spikes in pressure theprocess normally utilizes a transfer position corresponding to a 95–98% full cavity where the screwshifts from a constant velocity to a constant pressure control. Often injectiontimes are well under 1 second. Once the screw reaches the transfer position thepacking pressure is applied which completes mold filling and compensates forthermal shrinkage, which is quite high for thermoplastics relative to manyother materials. The packing pressure is applied until the gate (cavityentrance) solidifies. The gate is normally the first place to solidify throughits entire thickness due to its small size. Once the gate solidifies, no morematerial can enter the cavity accordingly, the screw reciprocates and acquiresmaterial for the next cycle while the material within the mold cools so that itcan be ejected and be dimensionally stable. This cooling duration isdramatically reduced by the use of cooling lines circulating water or oil froma thermolator. Once the required temperature has been achieved, the mold opensand an array of pins, sleeves, strippers, etc. are driven forward to de moldthe article. Then, the mold closes and the process is repeated A parting line,sprue, gate marks, and ejector pin marks are usually present on the final part.None of these features are typically desired, but are unavoidable due to thenature of the process. Gate marks occur at the gate which joins themelt-delivery channels (sprue and runner) to the part forming cavity. Partingline and ejector pin marks result from minute misalignments, wear, gaseousvents, clearances for adjacent parts in relative motion, and/or dimensionaldifferences of the mating surfaces contacting the injected polymer. Mold or dieare the common terms used to describe the tool used to produce plastic parts inmolding.Sincemolds have been expensive to manufacture, they were usually onlyused in mass production where thousands of parts were being produced. Typicalmolds are constructed from hardened steel, pre-hardened steel, aluminum, and/orberyllium -copper alloy. The choice of material to build a mold from isprimarily one of economics; in general, steel molds cost more to construct, buttheir longer lifespan will offset the higher initial cost over a higher numberof parts made before wearing out. Pre-hardened steel molds are less wear-resistantand are used for lower volume requirements or larger components; their typicalsteel hardness is 38–45 on the Rockwell-C scale. Hardened steel molds are heat treatedafter machining; these are by far the superior in terms of wear resistance andlifespan. Typical hardness ranges between 50 and 60 Rockwell-C (HRC). Aluminummolds can cost substantially less, and when designed and machined with moderncomputerized equipment can be economical for molding tens or even hundreds ofthousands of parts. Beryllium copper is used in areas of the mold that requirefast heat removal or areas that see the most shear heat generated. The moldscan be manufactured either by CNC machining or by using electrical dischargemachining processes.
Table.A.1 Fits and Tolerance
S.No
Description
Type of Fit
Tolerance
1
Main Guide pillar-Main guide bush
close running fit
H7 / g6
2
Sprue bush-Cavity plate
Medium drive fit
H7 / m6
3
Core pin-Core plate
Slide fit
H7 / h6
4
Push back pin-Core plate
Close running fit
H7 / g6
5
Ejector pin-Core plate
Close running fit
H7 / g6
6
Ejector Guide pillar-Ejector guide bush
Close running fit
H7 / g6
7
Register ring-Machine platen
Running fit
H7 / f7
The injection molding process can be brokeninto three phases, (1)Filling phase: During the filling phase plastic isinjected into the cavity is just filled. When designing a part to be made bythe injection molding process, the most important phase to as plastics flowsinto cavity, in contact with the mold wall freezes quickly. This creates afrozen layer of plastic between the mold and molten plastic. The flow frontscome into contact with the mold and freezes. The molecules in the frozen layerare therefore not highly oriented, and once frozen, the orientation will notchange. The Frozen layer gains heat as more molten plastic floes through thecavity and loses heat to the mold. When the frozen layer reaches a certainthickness, equilibrium is reached. This normally happens early in the injectionmolding process, after a few tenths of seconds. (2) Pressurization phase, thepressurization phase begins after the cavity has just filled. Although all flowpaths should be filled by this stage, the edge and corners of the cavity maynot contain plastic. To completely fill out the geometry, extra plastic ispushed into the cavity during the pressurization phase. The polymer injectionlocation I indicated by the yellow cone and the plastic is green. Some time theconfidence of fill result does not predict a short shot, but still states thata good quality part cannot be molded. This is because the condition at the endof the filling phase is not suitable for the part to be adequately packedduring the pressurization phase.(3) Compensating phases:Plastic have a highvolumetric shrinkage, around 25% from average melt temperature to solid.Therefore more material must be injected into the cavity to compensate for theplastic shrinkage as it cools. This is the compensating phase.
A.4. Mould Die Design
When purchasingplastics mould steels, one looks, for Good machining properties, Good polishability, Good photo – etching properties, Good spark erosion properties, Safe,uncomplicated heat treatment, Minimum inclusion level, Consistently highquality, Technical assistance and advice in tool in manufacturing andapplication.. Essential characteristic of injection mold steel like Uniformstructure and freedom from internal, defects, Machinability Maximum freedomfrom distortion during heat treatment, Weld ability, Polish ability, Wearresistance and toughness, Steels for mould fall under two categories,Structural section of the mould, Medium carbon silicon killed forging qualitysteel with approximately 25% greater tensile strength then typical low carbonsteel. It is annealed to approximately 165BHN. It is stress relieved forminimum deformation during machining.AISI 4130 type alloy steel is suppliedpre-heated to approximately 300BHN to withstand the peening effect of flash. Ithas durability for heavy construction loads and long production runs. Componentmaterial is selected as NYLON-66, Nylon 66 is a polyamide made from adipic acidand hexamethylenediamine by polycondensation,NYLON-66 has Good toughness, Hightensile strength, High elasticity, Good heat resistance, Excellent wearresistance, Wrinkle proof and excellent chemical resistance.Shrinkage isinherent in the injection moulding process. Shrinkage occurs because thedensity of polymer varies from the processing temperature to the ambienttemperature. The shrinkage factor will depends on Plastic material, Processingcondition, Product design, Mould design. Shrinkage allowance of Nylon 66 is0.5% considered. The dimensions of the cam bush have been modified withconsidering shrinkage allowance as shown in Table 1. This total dimensions areincorporated in the mould designing of core and cavity plate.
Table.2 Dimensions of Cam bush with shrinkageallowance
S.
No
Component
Details
Actual dimension
in mm
0.5% shrinkage
allowance in mm
Total dimension
in mm
1
Diameter 1
65
0.325
65.325
2
Diameter 2
35
0.175
35.175
3
Diameter 3
28
0.14
28.14
4
Diameter 4
20
0.10
20.10
5
Diameter 5
7
0.035
7.035
6
Length 1
15
0.075
15.075
7
Length 2
15.5
0.0775
15.5775
8
Length 3
19
0.095
19.095
A.5. Simulation of CAM BUSH in InjectionMoulding Process
Analysis donefor the part “CAMBUSH” to study andcalculate the flow pattern, fill time and packing time by considering coolingsystem which will affect the part performance. Also determine the clamp forceand injection pressure requires for the mould which will help to select theexact injection moulding machine and approximate cycle time. Polymer selectedfor analysis is NYLLON-66.Cooling holes diameter is 12mm.Gate diameter is 1.25.The global mesh density setting defines the nominal edge length for elements.The smaller the global edge length, the larger the total number of element onthe model. The global setting is the single most important setting to get anacceptable mesh on the part. We can optionally also set a local mesh density onselected surfaces/regions created by importing geometry from, for example, anIGES, step, para solid, or native CAD format. This is typically done to ensurethat small details in the model are properly represented, while meshing most ofthe part with a lower mesh density to optimize the total number of elements.The mesh is a web that consists of elements, with each element containing anode at every corner. The mesh provides the basis for a mould flow analysis,where moulding properties are calculated at every node. The mesh typessupported by the software are midplane mesh, surface or fusion mesh, volumemesh. The Midplane mesh provides the basis for the Flow analysis. These meshesconsist of trinode triangular element that forms a one dimensionalrepresentation of the part, through its centre. Every moulding process issupported by the mid-plane mesh. The surface mesh provides the basis for theflow analysis. This mesh consist of a mixture of different types, includingregions with traditional midplane element and surface (double-skin) shellelements. The surface mesh can be 3 or 6 noded plane, straight-edged triangles.The volume mesh provides the basis for the 3D Flow analysis. These meshesconsist of 4 -noded, tri-element, solid tetrahedral elements. The density of themesh is the number of elements per unit area. In general, the more elementsthere are in the mesh, the more detailed the analysis results, but the longerthe analysis time. The mould flow fusion capability allows us to performdetailed analyses directly on a thin-wall, surface mesh model is imported fromMould flow plastic Advisers or an External CAD packages.. The connectors areinserted automatically at locations determined according to the geometricalfeatures of the model. A boundary edge is an element edge that is not connectedto any other elements. Boundary edges are valid in mid plane model but must notbe present in surface meshed fusion model. Boundary edges indicate holes ortears in the mesh and must be corrected either in the original CAD system usedto create the model, or using mesh editing tool in mould flow plastic in sight.Following these guidelines the mesh type suited for the component is a fusionmesh. Element used for meshing is 3noded triangular element. Meshed model canbe seen in below figure.
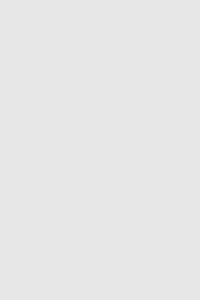
Fig A.3: Mesh Model
After meshing with a suitable mesh density,we may need to clean up the mesh .normally some cleanup is necessary if themesh was translated in from another system. MIP provides a mesh statisticsreport to check the quality of the mesh and a series of diagnostic displays tolocate and highlight specific problems. To clean up the mesh, there is a meshrepair wizard and a mesh tool box. The mesh repair wizard is an automated toolthat will find and fix most mesh problems.. To perform an analysis, we need toselect a suitable material in the material database. In most cases the materialto use will be prescribed so we need to locate that material in the databaseand use it for all analysis work. In other cases, one of the analysisobjectives may be to determine a suitable material. There are severaltechniques available to find a specific grade of material, assess the qualityof the material data, fine a substitute material, and compare materials withinthe select material dialog.
A.6. Runner Design
The fig shown below commonly used runner cross section shaped. Thefull-round runner is the best in terms of maximum volume-to-surface ratio,which minimizes pressure drop and heat loss. However, the tooling cost isgenerally higher because both halves of the mould must be machined so that thetwo semi-circular sections are aligned when the mould is closed.
Fig A.4: Commonly used Runner Cross-Section
The trapezoidal runner also works well andpermits the runner to be designed cut on one side of the mould. It is commonlyused in three plate moulds. Where the full -round runner may not be releasedproperly, and at the parting line in moulds, where the full interferes withmould sliding action. To compare runners of different shapes, the flowefficiency (L) of the melt through a runner, which is an index of flowresistance, is employed. The higher the flow efficiency of the melt through therunner, the lower the flow resistance is. Flow efficiency can be defined as L =A/P, Where L = flow efficiency of the melt through a runner. A = Cross sectionarea. P = perimeter. Once molten plastic has been injected into the mouldcavity, it takes time before the moulding has cooled and become sufficientlyrigid to allow it to be demoulded. This period is called the cooling time andoften forms a significant part of the moulding cycle. To allow a molded part tocool and solidify, heat must be removed from the mould. The cooling waterenters from one side of the plates, circulates and leaves. This normally refersto a fill analysis or a flow analysis. A fill analysis stops when the partvolume is just filled to 100%. The flow analysis is a fill analysis butcontinues through the packing and even cooling phases of the moulding cycle. Wecan identify and resolve a number of moulding issues using fill analysis beforerunning a flow analysis. Solving filling problems is typically an iterativeprocess requiring several analyses. Once the first fill analysis is done theresults are reviewed, and a problem is identified and fixed. This may requiremuch iteration of previous steps. There is one major assumption in the sequencedescribed here, namely, that the problem being addressed is a filling relatedproblem. And not packing, cooling or warpage related. The other problem, tooare solved by an iterative process, but only after the filling is optimized.Once the runner system is sized, packing of the part can be investigated.Although a flow analysis can be one without a gate or runner, it is not very muchrecommended. The freeze time of the gate and runners significantly affects thepacking of the part. Without a runner and gate, the packing analysis will beless accurate.
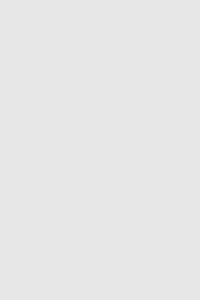
Fig A.5: Filling pattern of material into cavityand Air trap in component
Entrapped air in the mould can escapethrough air vents that are ground into the parting line of the mould. If thetrapped air is not allowed to escape, it is compressed by the pressure of theincoming material and is squeezed into the corners of the cavity, where itprevents filling and causes other defects as well. The air can become socompressed that it ignites and burns the surrounding plastic material. Weprovide vent holes to escape the compressed air after filling.We can produce auniform volumetric shrinkage with the use of a packing profile. The volumetricshrinkage distribution should be within 2%. When there is a uniform volumetricshrinkage across the part, the likelihood of warpage is reduced. Warpage issimply caused by a variation in shrinkage, therefore, when the shrinkagevariation is reduced, so is the warpage.The fill time result shows the positionof the flow front at regular intervals as the cavity fills. Each colors contourrepresents the parts of the mould which were being filled at the same time.
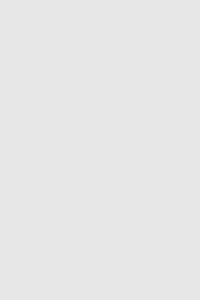
Fig A.6: Fill Time and Confidence of fill
The pressure at V/P switchover resultsshows the pressure distribution through the flow path inside the mould at theswitch over point from velocity to pressure control. Pressure should be zero atextremities of each flow path at the end of filling. The pressure drop occursas the cavity completing the filling and. The maximum pressure 0.8010Mpa isnoted.
Fig A.7: Pressure Drop and Temperature atflow front
Temperature at flow front result shows thetemperature of the polymer when the flow front reached specified point, in thecenter of the plastic cross- section. The flow front should not drop more thanthe range shown in fig during the filling phase. Large changes often indicatethat the injection time is too low, or there are areas of hesitation. If theflow front is too low in a thin area of the part, hesitation may result in ashort shot. In areas where the flow front temperature increases by severaldegrees, material degradation and surface defects may occur. At the start ofinjection the result temperature is 240.1 °C which shows in red colour and at end of injection the resulttemperature is 214.5 °C which shows in dark blue colour.
Fig A.8: Time to reach Ejection Temperature andWeld lines
Cycle-timeoptimization starts at design stage. Cooling time takes up over 50% of cycletime. Therefore understanding of cooling in the mould becomes very important.Injection molding is a cycle operation. The cycle consist of Mould closed andclamp, (few second- depends on machine speeds) Injection – Fill (speed) phases, (fewseconds) Switchover and pack (pressure) phases, (few seconds). Cooling time,(40 to 60% of cycle time) Actual filling time: 5.76 sec , Cool and pack time:396.50 sec ,Mold open: 5.00 sec , Total time: 407.25 sec. The clamping forceresult is a time-series result which shows the force of the mould clamp overtime. It is force resultant from filling and packing pressure that acts to openthe mould. The clamp force is a function of injection pressure and theprojected area of the part. A good clamping force results should show themaximum clamp force applied is less than 80% of the machine limits, allowingthe remaining 20% as a safety force. The clamp force result can producemisleading result if the model has overlapping surfaces is added. Use pressureprofiles or adjust part wall thickness to reduce the clamp force requirement.The maximum clamping force is noted as 0.194 tonnes.
A.7. Results and Discussions: The following result parameters that are obtained from theanalysis.
First Fill time:- 5.765 Sec
Cycle Time :- 407.25Sec
Injection Pressure:- 0.8010 Mpa
Injection Temperature:- 240.1°C
Average Temperature:- 240.0°C
Mold Temperature:- 40.0°C
Maximum Clamping Force :- 0.194tonnes
Holding Pressure:- 40 Bar
Clamping Pressure:- 60 Bar
Injection Time:- 1.5Sec
Cooling Time:- 60 Sec
Shot Weight :123grm
Injection Pressure:1486 Bar
Clamping Force :75tons
Distance between the bars:350 x 300mm
Mould thickness :125 - 310mm
Table A..3 Plastic Material Mechanical Properties
Materia
Specific gravity
Melting point (°F)
Melting point (°C)
Epoxy
1.12 to 1.24
248
120
Phenolic
1.34 to 1.95
248
120
Nylon
1.01 to 1.15
381 to 509
194 to 265
Polyethylene
0.91 to 0.965
230 to 243
110 to 117
Polystyrene
1.04 to 1.07
338
170
A.8. Mould Design CAM BUSH
Name of the components : CAM-BUSH
Material : NYLLON-66
Weight of the component : 66grm
Shrinkage Allowances : 0.5%
Average wall thickness of the mould : 15mm
Closed shut height of the mould : 250mm
Maximum day light : 610mm
Tool type : twoplate, two cavity mould
Distance between the tie bar : 350X 300 mm
Fig A.9: Solid Model of Cam Bush
Sprue Bushing: The maximum diameter of thesprue should be atleast 6mm in diameter. The minimum diameter should be greaterthan nozzle orifice by 0.5-1mm. The length of the sprue channel should be asshort as possible and never 100mm long. The sprue included angle has to be 4-5°. Design of runner: The mainconsideration for the designer to design a mould is the shape and cross sectionof the runner, the size of the runner and Layout of the runner. The differentshapes of the cross section of the runner are fully rounded, semicircular,trapezoidal, modified trapezoidal, hexagonal, square and rectangular. Semi-circular cross section type runner is selected because it is easy to machine.Runner diameter calculation: D = (√W *4√L)/3.7=(√66 *4√16)/3.7 = 4.39mm, D- Diameterof runner, L- Length of Runner = 16mm, W- Weight of Cam Bush= 66g.The temperatureof the mould must be maintained at some constant temperature below the heatpoint of the plastic, in order to chill it to a rigid state. Differentialcooling strains are set, if the mould temperature is not uniform and thosestrains may cause distortion of the moulding after ejection. The heat input issupplied by the injection heating cylinder to plasticize the material must beremoved from the mould to permit ejection.Q = m x {Cp x (Tmat – Tmould) + Lt }= 66 x {0.4x(240 – 40) +57.8}=9094.8cal/hr.
Cost Estimation
1. Mould Cost
Raw material (EN-353) = Total w.t of theEN-353 in the tool (Kg) x raw material cost per Kg = 78 x 140 = Rs10,920/-
Raw material (Mild Steel) = Total weight ofthe EN-36 in the tool (Kg) x raw material cost per Kg
= 230 x 85 =Rs 19,550/-
Raw material (OHNS) =Total weight of the OHNS in the tool (Kg) x raw material cost per Kg
= 40 x 115 =Rs 4,600/-
Total Raw material cost = 10,920 +19,550 +4,600 =Rs 35,070/-
2. Machining Cost
Machining cost = {(Milling hrs × Rs/hr) + (Polishing hrs × Rs/hr) + (drilling hrs × Rs/hr) + (Tapping hrs × Rs/hr) + (Surface Grinding hrs× Rs/hr) + (H. TRs/kg) + (CNC EDM hr × hr/kg) + (CNC Milling hrs × hr/kg) + (CNC Wire cut ×Rs/hr)}= {(45 x 200) + (18 x 250) + (9 x 225) + (4 x 225) + (15 x 400)+ (80 x 150) + (50 x 300) + (74 x 650) + (3 x250)}= {9,000 + 4,500 +2,025 + 900+ 6,000 + 12,000 + 15,000 + 48,100 + 750} = Rs 98,275/-
Design Cost = Totaldesign hours ×cost/hr = 40 x 400 = Rs 16,000/-
Electrode (copper) material & machiningcost = Rs 5000/-
Standard Items Cost = Rs5000/-
Mould assembly cost = Assembly hr. × Labour cost = 10 x 130 = Rs1300/-Trial cost = Total Trial hr× trial cost/ hr =10 x 400=Rs 4000/-
Total cost = (Raw material cost + Machiningcost + Design cost+ Electrode Material + Standard items + Mould Assembly cost +Trial cost ) = (35,070+ 98,275+ 16,000+5000 + 5000 + 1300 + 4000) = Rs 1,64,645/-Company profit = 15% of the Total Cost = 15% x 1, 64,645 = Rs 24,696/-
Total cost of the die = Total cost +Company profit = 1, 64,645 + 24,696 , Total cost of the die = Rs 1, 89,341/-
FigA.10: Solid Model of Mould Die and ExplodedView
Fig A.11: Core for Cam Bush and Cavity forCam Bush
A.9. Conclusion
The dies havebeen designed by using Unigraphics software for the Modling of the Die.Variousfactors were considered to produce a defect free and economical plasticcomponent during the design stage itself. The ejection of the component is mucheasier; the cost and cycle time is reduced. Autodesk Mould Flow Insight softwareis used for analyzing the component. To see the possible defect and optimizethe design to achieve the maximum outcome of the product with minimum cycletime in each production cycle. The Molding process condition like InjectionFill time, Injection pressure, Temperature at Flow front, Time to reachejection temperature etc. are analyzed well within the limit. The Result areFirst Fill time: 5.765 Sec, Cycle Time is 7.25Sec, Injection Pressure as 0.8010Mpa, Injection Temperature 240.1°C, Clamping Pressure as 60 Bar. SuggestionAlternate Material for CAM BUSH for better strength. Production Rate canincrease by designing the existing product with multi-cavity layout and withthis production time can reduce. By modifying the Tool Material, the Tool cost canbe reduced.
附录B 中文翻译
塑料注塑模具设计与分析凸轮轴衬潜伏浇口
B.1. 介绍
现在一天的塑料的日常生活中占据了至关重要的作用。不夸张的说,如果我们说没有领域,塑料没有介入的制造业在销的飞船。在19世纪中期,塑料开始主导作用在材料和我们的生活。耐腐蚀的一些方面,塑料甚至成为上级金属和获得率升高的偏好在生产的每一个分支。从塑料的紧急情况来看,它们在塑料制品的设计、制造加工、测试领域等各个方面正经历着激烈的发展,现在,由于许多人的努力,最终通过人工劳动来完成,但在人工智能的帮助下。也就是说,像CAD/CAM这样的软件包。由于重量比高,提高了耐化学性和耐温性,镀液的耐热性和耐腐蚀性,透明性使它们成为材料的选择。塑料在成型过程中消耗较少的能量,并且可以有效地回收利用。今天,塑料正在取代金属如黄铜、铜、铸铁、钢等。塑料可以根据制造方法分为主要组:那些在加热时软化并在冷却时凝固的塑料。这些被称为“热塑性塑料”和那些由于化学变化而被加热时硬化的材料。这些被称为热固性或杜洛塑料材料“选择特定材料的产品是另一个重要因素。这对于产品的确定尤其必要。它也应该能够承受作用在它上的应力。每种材料都有自己的属性和属性。有些材料在较高的环境下具有优异的耐磨性。困难的部分是找到一个材料,将接近满足整个目的的要求。所以材料应该是多才多艺的,它符合我们产品的所有考虑和要求。在考虑所有这些点之后,必须选择合适的材料来满足所有这些条件。
B.2变压器用塑料凸轮衬套
本文的目的是对高压变压器凸轮布什的注塑模工具进行设计和分析。Cam Bush用作高压变压器开/关分接开关装置中的分度装置,用作分度头和换能齿轮之间的连接件。分度头通过与凸轮衬套相连的轴与齿轮连接。凸轮布什有两个尾端,一个侧面被压装到分度曲柄圆圈上,另一侧安装在驱动机构上。每个孔具有不同的驱动机构,当分度圆旋转并且曲柄销接合在第一孔中时,第一驱动机构打开。通过改变索引位置来获得不同类型的功率。Cam bush用作曲柄圆圈与齿轮之间的连接件。它是在功率变化的分度机构中提供的。分度曲柄圆圈有多个分度孔,但机构有6个传动机构,因此在曲柄圈、速度指示器轮和中心交叉的轴之间设有6个孔的凸轮布什,并与齿轮连接。这种凸轮衬套一般用聚苯乙烯、尼龙6和聚氯乙烯制成。由于高电压调节应用,这个Cam Bush变热并磨损。由于反复施加压力通过调节它,它就变成了损坏。
B.1固体模型和电影凸轮衬套装配
塑料是人造材料。它们比玻璃更脆,但也可以同样透明和光滑。它们重量轻,同时具有良好的强度和刚度。它们抵抗腐蚀和化学物质的作用。它们可以很容易地模制成不同的形状。常用的热塑性材料有聚苯乙烯、尼龙6、P.V.C、聚丙烯等。模具制造在塑料工业中占有重要地位,因为相关产品占消费产品中70%以上的成分。注射成型是一种复杂而高效的生产多种热塑性产品的方法,具有生产周期短、产品表面优良、无二次操作、成型复杂形状等优点。复杂塑料制品注射成型工具的设计和制造,在满足工业需求,尤其是塑料工业中发挥着更大的作用。因此,在工业上需要能够生产塑料部件的塑料注射成型技术。文献回顾表明,目前对复杂塑件注塑模具设计和制造的研究还比较缺乏。因此,本课题主要针对凸轮布什的挡板式冷却通道和潜流浇口的注射成型模具进行设计和分析。
B.3注射成型工艺
这是一种通过将液体熔融材料注射到模具中生产零件的制造工艺。注射成型可以用大量的材料进行,包括金属、玻璃、弹性体、糖果和最常见的热塑性和热固性聚合物。该部件的材料被喂入加热的桶中,混合,并被迫进入模具腔,在该腔中冷却并硬化到空腔的配置。在设计产品后,通常由工业设计师或工程师,模具由模具制造商(或工具制造商)从金属制成,通常是钢或铝,并精密加工以形成所需零件的特征。注塑成型被广泛用于制造各种零件,从最小的部件到汽车的整个车身板。零件,所需的形状和特征的部分,模具的材料,以及成型机的性能都必须考虑在内。通过这种设计考虑和可能性,注塑成型的通用性得到了便利。注射成型采用了一个冲压或螺旋式柱塞,迫使熔融塑料材料进入模具腔;这凝固成一个符合模具轮廓的形状。这是最常用的处理热塑性和热固性聚合物,前者是相当丰富的年度材料量处理。
图B.2:注塑成型模型
注射成型包括将原料高压注射到模具中,模具将聚合物成形为所需形状。模具可以是单腔或多个腔。在多个腔模中,每个腔可以是相同的并且形成相同的部分,或者可以是唯一的并且在一个周期内形成多个不同的几何形状。模具通常由工具钢制成,但是不锈钢和铝模具适合于某些应用。铝模具通常不适合大批量生产或具有窄尺寸公差的零件,因为它们具有较低的机械性能,并且在注射和夹紧循环期间更容易磨损、损坏和变形;但在低体积应用中是具有成本效益的。随着模具制造成本和时间大大减少。许多钢模具的设计过程中加工超过一百万个部分,在他们的一生中,可以花费几十万美元制造。当热塑性塑料被模制时,典型的粒状原料通过料斗被送入加热的桶中,并带有往复螺杆。在进入筒体时,由于较高的热能状态下分子之间的空间增大,热能增加,并且阻止单个链的相对流动的Vander Waals力减弱。这降低了其粘度,这使得聚合物能够与注射单元的驱动力一起流动。螺杆将原材料向前输送,混合并均匀地分配聚合物的热和粘性分布,并通过机械地剪切材料并向聚合物中加入大量的摩擦加热来减少所需的加热时间。该材料通过单向阀向前进给,并在螺杆的前端收集到一个称为喷射的体积。喷丸是用来填充模具腔的材料体积,补偿收缩,并提供缓冲(约10%的总喷射体积保持在筒中并防止螺杆从底部冲出),以将压力从螺杆传递到模具腔。当收集到足够的材料时,材料在高压和速度下被迫进入零件成形腔。为了防止压力中的尖峰,该过程通常利用对应于95至98%全腔的转移位置,其中螺杆从恒定速度转移到恒压控制。注射时间通常在1秒以下。一旦螺杆到达转移位置,施加填充压力,完成模具填充并补偿热收缩,这对于热塑性塑料相对于许多其他材料来说是相当高的。施加填料压力直到浇口(腔入口)凝固为止。浇口通常是由于其小尺寸而通过其整个厚度固化的第一位置。一旦浇口固化,没有更多的材料可以进入空腔,螺杆往复运动,并在下一个循环中获得材料,而模具内的材料冷却,从而可以喷射并尺寸稳定。通过使用来自热风炉循环水或油的冷却线,这种冷却时间显著减少。一旦达到所需的温度,模具打开,销、套筒、汽提塔等的阵列被向前驱动以使制品脱模。然后,模具闭合并重复该过程,在最后部分上通常存在分型线、浇口、浇口标记和顶出销标记。这些特征通常不是所期望的,但由于过程的性质是不可避免的。浇口标记出现在浇口处,熔体输送通道(浇道和浇道)与零件成型腔连接。分型线和顶出针标记是由微小的错配、磨损、气门、相对运动的相邻部件的间隙和/或与注入聚合物接触的配合表面的尺寸差异引起的。模具或模具是用来描述模具中用来生产塑料零件的常用术语。由于制造成本很高,它们通常只用于批量生产,其中有成千上万的零件被生产。典型的模具是由淬火钢、预硬化钢、铝和/或铍铜合金构成的。从模具制造材料的选择主要是经济学的;一般来说,钢模花费更多的构造,但其更长的使用寿命将抵消较高的初始成本比在磨损之前制造的零件的数量更多。预硬化钢模具的耐磨性较差,用于较低的体积要求或更大的部件;它们的典型钢硬度在洛氏C级上为38~45。淬硬钢模具经过加工后经过热处理,在耐磨性和寿命方面都是优越的。典型的硬度范围在50和60洛氏C(HCC)之间。铝模可以大大降低成本,并且当用现代计算机设备设计和加工时,可以很好地成型几十个甚至数十万个零件。铍铜用于模具领域,需要快速散热或看到最多的剪切热产生的区域。模具可以通过CNC加工或使用放电加工工艺来制造。
B.1配合和公差
序号
描述
拟合类型
公差
1
主导柱主导布什
近距离配合
H7 / g6
2
浇道套板
中等传动配合
H7 / m6
3
芯销芯板
滑动配合
H7 / h6
4
后推销芯板
近距离配合
H7 / g6
5
顶出芯板
近距离配合
H7 / g6
6
喷射器导柱喷射器导向器布什
近距离配合
H7 / g6
7
定位环机压板
转动配合
H7 / f7
注射成型过程可分为三个阶段,(1)填充阶段:在填充阶段,塑料注入空腔中正好填充。当设计一个由注塑工艺制造的零件时,最重要的阶段是随着塑料流入腔,与模具壁接触迅速冻结。这就在模具和熔融塑料之间形成了一层冻结的塑料。流动前沿与模具接触并结冰。因此,冷冻层中的分子不是高度取向的,一旦冻结,取向就不会改变。当更多的熔融塑料流过空腔并且失去热量到模具时,冻结层获得热量。当冻结层达到一定厚度时,达到平衡。这通常发生在注射成型过程的早期,几秒钟后。(2)加压阶段,加压阶段在空腔刚刚填充之后开始。虽然所有的流动路径都应该由这个阶段填充,但是空腔的边缘和角落可能不包含塑料。为了完全填充几何形状,在加压阶段,额外的塑料被推入空腔中。用黄色圆锥体和塑料表示的聚合物注入位置是绿色的。有些时候,填充结果的置信度不能预测短镜头,但仍然表示质量好的部分不能成型。这是因为在填充阶段结束时的条件不适合于在加压阶段充分包装的部分。(3)补偿阶段:塑料具有高的体积收缩率,从平均熔体温度到固体的约25%。因此,必须将更多的材料注入到空腔中,以补偿冷却时的塑性收缩。这是补偿阶段。
B.4模具设计
在购买塑料模具钢时,一方面表现出良好的加工性能、良好的抛光性能、良好的光蚀性能、良好的火花腐蚀性能、安全、不复杂的热处理、最低的夹杂物水平、一致的高质量、技术上的辅助和工具上的建议。制造与应用注塑模具钢的基本特征,如均匀的结构和自由的内部、缺陷、Machinability Maximum在热处理过程中的自由变形、焊接能力、抛光能力、耐磨性和韧性、两种类型的铸钢落钢、结构部分在模具中,中碳硅镇静锻钢的抗拉强度约为25%,然后是典型的低碳钢。它被退火到大约165BHN。在加工过程中,应力消除最小。AISI 4130型合金钢被预热至约300 BHN,以承受闪光的喷丸效果。它具有耐用的重型建筑负荷和长生产运行。尼龙66是由己二酸和六亚甲基二胺经缩聚制得的聚酰胺,尼龙66具有良好的韧性、高抗拉强度、高弹性、良好的耐热性、优异的耐磨性、抗皱性和优异的耐化学性。收缩是注塑成型过程中固有的。收缩是因为聚合物的密度从加工温度到环境温度而变化。收缩系数将取决于塑料材料、加工条件、产品设计、模具设计。尼龙66的收缩余量为0.5%。如表1所示,考虑了收缩余量对凸轮衬套的尺寸进行了修改。这些总尺寸被纳入芯模和型腔板的模具设计中。
表2具有收缩余量的Cam bush的尺寸
序号
成分细节
实际尺寸/mm
0.5%允许收缩 /mm
总尺寸/ mm
1
直径1
65
0.325
65.325
2
直径 2
35
0.175
35.175
3
直径 3
28
0.14
28.14
4
直径 4
20
0.10
20.10
5
直径 5
7
0.035
7.035
6
长度 1
15
0.075
15.075
7
长度 2
15.5
0.0775
15.5775
8
长度 3
19
0.095
19.095
B.5注塑过程中凸轮衬套的仿真
对“凸轮衬套”部分进行了分析,通过考虑冷却系统对零件性能的影响,研究并计算了流型、填充时间和填料时间。还确定模具的夹紧力和注射压力,这将有助于选择精确的注塑机和近似的循环时间。分析选用的聚合物为尼龙6,冷却孔直径12mm,浇口直径为1.25。全局网格密度设置定义元素的标称边缘长度。全局边缘长度越小,模型上的元素总数越大。全局设置是在部件上获得可接受网格的唯一最重要的设置。我们还可以可选地通过从IGES、STEP、PARA实体或本机CAD格式导入几何形状创建的选定表面/区域上设置局部网格密度。这通常是为了确保模型中的小细节被适当地表示,而以较低的网格密度对大部分部件进行网格化,以优化元素的总数。网格是一个由元素组成的网络,每个元素在每个角落都包含一个节点。网格提供了模具流动分析的基础,其中在每个节点计算成型特性。软件支持的网格类型为中面网格、曲面或融合网格、体网格。中面网格为流动分析提供了依据。这些网格由三角形三角形元素组成,通过其中心形成部分的一维表示。每一个成型过程都由中面网格支撑。表面网格为流动分析提供了依据。该网格由不同类型的混合物组成,包括具有传统中面单元和表面(双皮)壳单元的区域。表面网格可以是3或6个点状平面,直边三角形。体积网格为三维流动分析提供了依据。这些网格由4个点阵、三个元素、立体四面体元素组成。网格的密度是每单位面积的元素数。一般来说,网格中的元素越多,分析结果越详细,但分析时间越长。模具流动融合能力允许我们直接在薄壁上进行详细的分析,表面网格模型是从模具流动塑料顾问或外部CAD软件包导入的。连接器在根据模型的几何特征确定的位置自动插入。边界边缘是不与任何其他元素相连的元素边缘。边界边缘在中面模型中是有效的,但在表面网格融合模型中不一定存在。边界边缘指示网格中的孔或撕裂,并且必须在用于创建模型的原始CAD系统中进行校正,或者在网格流动塑料中使用网格编辑工具。遵循这些准则,适合于组件的网格类型是融合网格。用于网格划分的元素是3NOD三角形元素。网格模型可以在下图中看到。
图B.3:网格模型
用合适的网格密度进行网格划分后,我们可能需要清理网格。通常,如果将网格从另一个系统中转换,就需要进行一些清理。MIP提供网格统计报告来检查网格的质量和一系列诊断显示,以定位和突出特定的问题。为了清理网格,有一个网格修复向导和一个网格工具箱。网格修复向导是一个自动工具,可以找到并修复大多数网格问题。为了进行分析,我们需要在材料数据库中选择合适的材料。在大多数情况下,使用的材料将被规定,所以我们需要定位数据库中的材料,并将其用于所有的分析工作。在其他情况下,分析目标之一可以是确定合适的材料。有几种技术可用于寻找特定级别的材料,评估材料数据的质量,精细替代材料,并在选择材料对话框中比较材料。
B.6 流道设计
图中所示的常用流道横截面形状。全轮转轮是最大的最大体积比,最大限度地减少压降和热损失。然而,模具成本通常较高,因为模具的两个半部都必须被加工,使得两个半圆形部分在模具闭合时对齐。
图B.4:常用的转轮横断面
梯形转轮也能很好地工作,并允许流道设计在模具的一侧。它通常用于三个板模具。在整个圆周转轮可能无法正确释放,并在模具的分型线,其中充分干扰模具滑动作用。为了比较不同形状的流道,采用了流道的流动效率(L),该流道是流动阻力的指数。熔体通过流道的流动效率越高,流动阻力越低。流动效率可以定义为L=A/P,其中L=熔体通过流道的流动效率。A=横断面面积。P=周长。一旦熔融塑料被注射到模具腔中,在模制冷却之前需要时间,并且变得足够刚性以使其脱模。这个时期被称为冷却时间,并且常常形成模塑周期的重要部分。为了使模制部件冷却和固化,必须从模具中取出热量。冷却水从板的一侧进入,循环和离开。这通常指的是填充分析或流分析。当部分体积正好填充到100%时,填充分析停止。流动分析是填充分析,但通过模塑循环的包装和冷却阶段继续进行。在运行流分析之前,我们可以使用填充分析来识别和解决多个造型问题。解决填充问题通常是一个需要多次分析的迭代过程。一旦完成第一次填充分析,就对结果进行回顾,并确定并固定问题。这可能需要多次迭代先前的步骤。在这里描述的序列中有一个主要假设,即,所处理的问题是与填充有关的问题。而不是包装,冷却或翘曲相关。另一个问题也是通过迭代过程来解决的,但是只有在填充被优化之后。一旦浇注系统的尺寸,包装的部分可以进行调查。虽然流量分析可以是一个没有浇口或流道,但它不是很推荐。浇口和流道的冻结时间对零件的包装有很大的影响。如果没有浇口和浇口,填料分析就不那么精确了。
图B.5:材料进入模腔和空气阱的填充模式
在模具中夹住的空气可以通过进入模具分型线的排气口逸出。如果被困的空气不允许逃逸,它被进入材料的压力压缩,并被挤压到空腔的角落,在那里它防止填充,并导致其他缺陷。空气会变得如此压缩以至于点燃并燃烧周围的塑料材料。在充填后,我们提供排气孔来逃避压缩空气。我们可以通过使用填充轮廓来产生均匀的体积收缩。体积收缩分布应在2%以内。当在整个部件上有均匀的体积收缩时,翘曲的可能性降低。Warpage仅仅是由于收缩的变化引起的,因此,当收缩变化减小时,翘曲也是如此。填充时间的结果表明,当空腔填充时,流动前沿的位置以规则的间隔出现。每一种颜色轮廓代表了同时填充的模具的部分。
图B.6:填充时间和填充量的置信度
在V/P切换的压力结果示出了通过在模具内的流动路径的压力分布在切换点从速度到压力控制。充填结束时各流道末端的压力应为零。压降发生在空腔完成填充时。注意到最大压力0.8010MPa。
图B.7:流动前沿的压降和温度
流动前沿的温度显示了聚合物在流动前沿到达指定点时在塑料横截面中心处的温度。在填充阶段,流动前沿不应下降超过图中所示的范围。大的变化常常表明注射时间太低,或者有犹豫的区域。如果流线在零件的薄区域太低,犹豫可能导致短射程。在流动前沿温度增加几度的区域,可能发生材料退化和表面缺陷。在注射开始时,结果温度为240.1°C,呈红色,注射结束时,温度为214.5°C,呈深蓝色。
图B.8:到达喷射温度和Weld线的时间
循环时间优化从设计阶段开始。冷却时间占循环时间的50%以上。因此,理解模具中的冷却变得非常重要。注塑成型是一种循环操作。该循环包括模具闭合和夹紧,(少数秒取决于机器速度)注入-填充(速度)阶段,(几秒钟)切换和包装(压力)阶段,(几秒钟)。冷却时间,(40至60%的循环时间)实际填充时间:5.76秒,冷却和包装时间:396.50秒,模具打开:5秒,总时间:407.25秒。夹紧力的结果是一个时间序列的结果,显示了模具钳的力量随着时间的推移。充模压力和填料压力共同作用于打开模具。夹紧力是注射压力和零件投影面积的函数。良好的夹紧力结果应该表明施加的最大夹紧力小于机器极限的80%,使得剩余的20%作为安全力。当模型具有重叠表面时,夹紧力的结果会产生误导的结果。使用压力分布或调整零件壁厚以减少夹紧力要求。最大夹紧力为0.194吨。
B.8 模具设计凸轮衬套
组件名称:CAM-BUS
材料:尼龙66
组件重量:66GRM
收缩余量:0.5%
模具平均壁厚:15mm
模具闭合高度:250mm
最大日照量:610mm
工具类型:双板双腔模具
系杆间距:350×300 mm
图B.9: Cam Bush的实体模型
浇道衬套:浇口的最大直径应至少为6mm直径。最小直径应大于喷嘴孔0.5~1mm。浇口通道的长度应尽可能短,且不能长100mm。浇口夹角必须为4-5°。转轮设计:设计者设计模具的主要考虑因素是转轮的形状和横截面、转轮的尺寸和转轮的布置。转轮横截面的不同形状是完全圆的、半圆形的、梯形的、梯形的、六边形的、正方形的和矩形的。半圆形截面式流道因其易加工而被选用。转轮直径计算:D=(Φ4×L)/ 3.7=(66×4×16)/3.7=4.39 mm,转轮直径D,流道L长度=16mm,凸轮轴瓦W重量=66克。模具的温度必须保持在低于塑料的热点的恒定温度,以使其冷却至A。刚性状态。如果模具温度不均匀,则这些差动冷却应变被设定,并且这些应变可能导致喷射后成型的变形。热输入由注射加热筒提供,使材料塑化,必须从模具中取出以允许喷射。Q=M×{CPX(TMAT -TMID)+Lt}=66×{0.4X(240 - 40)+57.8 }=9094.8CAL/HR。 成本估算
1.模具成本 原材料(EN-353)=工具中的EN-353的总重量(kg)x原料成本每公斤=78×140=RS10920/-
原材料(软钢)=工具中的E-36总重量(kg)×每公斤原料成本 =230×85=RS 19550/-
原材料(OHNs)=工具中的OHN的总重量(kg)x每公斤原料成本 =40×115=RS 4600/-
总原料成本=10920+19550+4600=RS 35070/-
2.加工成本 加工成本=铣削HRS×RS/HR+(抛光HRS×RS/HR)+(钻孔HRS×RS/HR)+(研磨HRS×RS/HR)+(表面磨削HRS×RS/HR)+(H. T Rs /kg)+(CNC EDM HR×HR/kg)+(CNC铣削HRS×HR/kg)+(CNC线切割×RS/HR)}={(45×200)+(18×250)+(9×225)+(4×225)+(15×400)+(80×150)+(50×300)+(74×650)+(3×250)}=RS98275/
设计成本=总设计小时×成本/HR=40×400=RS 16000/
电极(铜)材料和加工成本=RS 5000/
标准项目成本=RS 5000/
模具装配成本=装配人力资源。×人工成本=10×130=RS 1300/-试验成本=总试验HR×试验成本/HR=10×400=RS 4000/-
总成本=(原材料成本+加工成本+设计成本+电极材料+标准项目+模具装配成本+试验成本)=(35070+98275+16000+5000+5000+1300+4000)=RS 1, 64645/-公司利润=15%总成本=15%×1,64645=RS 24696/
模具总成本=总成本+公司利润=1, 64645+24696,模具总成本=RS 1, 89341/-
图B.10:模具的实体模型和开模视图
图B.11: Cam Bush的核心和Cam Bush的腔
B.9 结论
采用UngpHICS软件对模具进行模具设计,在设计阶段考虑各种因素,产生无缺陷、经济的塑件。组件的喷射更容易,成本和周期时间都减少了。Autodesk模具流洞察软件用于分析组件。在每一个生产周期中,找出可能出现的缺陷并优化设计以达到产品的最小周期时间的最大结果。对注塑成型工艺条件如注塑充型时间、注射压力、流道前沿温度、喷射温度时间等进行了分析。结果为首次充注时间:5.765秒,循环时间为7.25s,注入压力为0.8010 MPa,注入温度为240.1°C,夹持压力为60巴。建议更换凸轮衬套材料以获得更好的强度。通过对现有的多腔布局产品的设计,可以提高生产速度,减少生产时间。通过改变刀具材料,可以降低刀具成本。