The ultrasonic bonding process typically started by feeding the wire at an angle usually 30-60° from the horizontal bonding surface through a hole in the back of a bonding wedge. Normally, forward bonding is preferred, i.e. the first bond is made to the die and the second is made to the substrate. The reason is that it can be far less susceptible to edge shorts between the wire and die. By descending the wedge onto the IC bond pad, the wire is pinned against the pad surface and an U/S or T/S bond is performed. Next, the wedge rises and executes a motion to create a desired loop shape. At the second bond location, the wedge descends, making a second bond. During the loop formation, the movement of the axis of the bonding wedge feed hole must be aligned with the center line of the first bond, so that the wire can be fed freely through the hole in the wedge. Several methods can be used to end the wire after the second bond. For small wires (<.003”/76µm), clamps can be used to break the wire while machine bonding force is maintained on the second bond (clamp tear), or the clamps remain stationary and the bonding tool raises off the second bond to tear the wire (table tear). The clamp tear process offers a slightly higher yield and reliability than the table tear process due to the force maintained on the second bond during the clamp tear motion. The clamp tear process also offers a slight speed advantage over the table tear process due to fewer required table motions. However, the table tear process, has a higher wire feed angle capability and stationary clamp, has the potential to provide slightly more clearance from package obstructions such as a bond shelf or pin grid. For large bonding wires (>.003”/76µm), the most common method is using a cutter blade. Once the wire is terminated, the wedge ascends. The clamped wire is fed under it to begin bonding the next wire…this process will repeat until the wire bond program is complete.
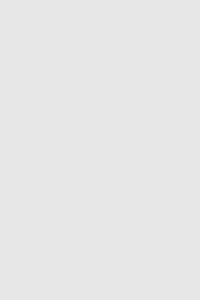
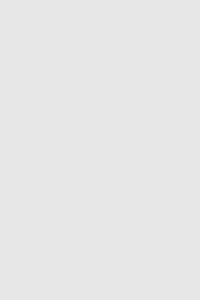
Clamp Tear
Table Tear
Guillotine termination methods
Wedge bonding technique can be used for both aluminum wire and gold wire bonding applications with some slight modification to the back radius to compensate for the lower tensile strength of gold wire. The principle difference between the two processes is that the aluminum wire is bonded in an ultrasonic bonding process at room temperature, whereas gold wire wedge bonding is performed through a thermosonic bonding process with heat up to 175°C. A considerable advantage of the wedge bonding is that it can be designed and manufactured to very small dimensions, down to 50µm pitch. Aluminum ultrasonic bonding is the most common wedge bonding process because of the low cost and can be bonded at room temperature. The main advantage for gold wire wedge bonding is the possibility of avoiding the need for hermetic packaging after bonding due to the inert properties of the gold. In addition, a wedge bond will give a smaller footprint than a ball bond, which specially benefits the microwave devices with small pads that require a gold wire junction down to .0005”/ 13µm.
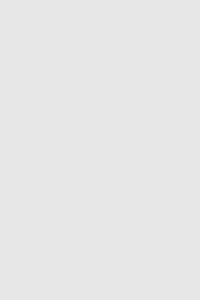
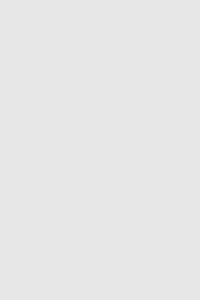
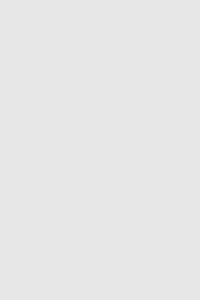
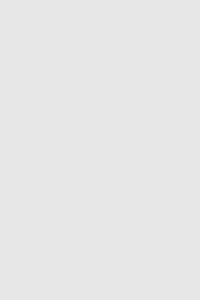
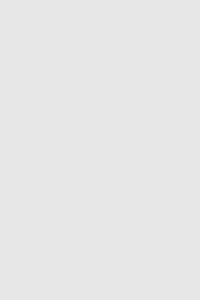
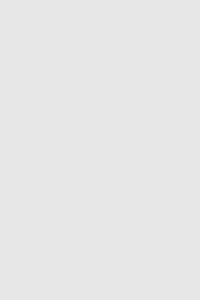
本站仅提供存储服务,所有内容均由用户发布,如发现有害或侵权内容,请
点击举报。