印染厂水网系统的优化及节水措施
尹华,郭华芳,何兆红,鲁涛
摘要:对印染厂的水网系统进行优化,发现中水回收与逐格倒流节水技术有很好的节水效果;在节水工艺中,冷轧堆前处理工艺的节水效果最好,其次分别为冷轧堆染色、涂料染色和涂料印花工艺。
关键词:染整;节约;水;水网系统;工艺流程
Optimization of water system and water saving processes in dyehouse
YIN HuaIGUO Hua—fang,HE Zhao—hong,LU Tao
Abstract:Water reticulation system in dyehouse is optimized.Experimental results in dicate that reclaimed water recycling and counter flow technologies have a good water-saving effect.The cold pad-batch pretreatment process has the lowest water consumption,followed by the cold pad-batch dyeing。Pigment dyein gandpigment printing process.
Keywords:dyeing and finishing;save;water;water reticulation system;process
O前言
据国家统计局统计,2000—2009年,我国淡水资源总量约2.8万亿m3,人均淡水资源约2160m3,人均可利用淡水资源仅900m3,成为世界严重缺水的国家之一。目前,全国655个城市中,400多个缺水,其中ll0个严重缺水,再加上人为因素所致的水污染问题,使得我国水资源贫乏的形势更加严峻。2008年,全国废水排放总量为571.7亿t,比2007年增加2.7%。其中,工业废水排放量为241.7亿t,占废水排放总量的42.3%,严重污染长江、黄河、淮河等重大流域,造成污染性缺水问题。
纺织印染行业是工业取水量及排污量很大的行业之一。据不完全统计,中国纺织行业的年耗水量达95.48亿t,居全国各行业第2位,废水排放量居全国第6位(其中印染废水占全国纺织废水排放量的80%)[1]。因此,在印染行业进行节水清洁生产研究,节省新鲜水的使用量,减少污水排放量,对缓解我国水资源的短缺问题具有非常重大的意义。
印染行业节水清洁生产的方法有很多,但主要是在加强生产管理的前提下,加强回用技术的应用,实行工艺变量的在线控制,在优化水网系统和生产工艺的同时,采用高效助剂和先进设备[2]。限于篇幅,本文仅从优化印染厂水网系统和工艺流程着手,通过典型的节水案例,为印染企业改进节水生产工艺提供参考。
1水网系统的优化
纺织印染厂虽然用水量大、水网系统复杂,但只要仔细对工厂的供水、排水系统进行系统规划与设计,认真考虑,统一协调供水、排水、污水回用等水系设施及其它基础设施,完全可以减少清洁水的消耗和废水的排放。
1.1案例一
某公司年产3000万ITI各类织物的印花、染色产品。主要用水设备有皂洗机、氧漂机、丝光机、水洗机、定形机、印花机等。为了减少新鲜水的取水量,减少企业运行成本,从2000年开始,公司就开始对水网系统实行优化,并取得如表1所示节水效益。水网系统优化的总思路和具体措施如下:
(1)水网系统优化的总思路
以把握生产回用水水质要求为前提,对退浆、煮练、漂白、染色、印花、漂洗、整理等各个工序的生产用水水质要求和冷却水水质要求进行调研和测试,在此基础上,针对不同工序对水质的不同要求,实现废水的重复多次利用,实现水网系统的最优化。
(2)水网系统优化的具体措施(见表1)

①将污水厂尾水深度处理,年回收中水150×104t,其950×l04t用于公司后整理成品车间的冷却用水和水洗车间水洗场的水洗用水等。
②采用逐格倒流节水技术,针对不同工序对水质的不同要求,将后一道工序的排水用于上一道工序的漂洗用水,逐级逆向多次重复利用。例如,将丝光工序废水过滤后用于煮练的部分水洗;回收丝光扩容蒸馏水用于煮练部分水洗、部分设备除尘和清洗;将染色工序部分洗涤废水与其它污染程度轻的废水混合处理后用于前处理的退浆工序;将皂洗、固色阶段洗涤废水处理后回用于前处理阶段。
③将染色机、定形机等用汽设备的冷凝水全部回用于电厂的锅炉用水。
④将定形机、染色机的直接冷却水全部回收到储水池进行重复利用。
⑤在氧漂机、水洗机、皂洗机、丝光机上分别安装热交换器和循环过滤器,实现冷却水封闭式循环利用。
由表l可知,该公司在优化水网系统中,通过污水厂尾水深度处理技术(即中水回用)取得的节水效益最好,年节水为50×104t,占总节水量的45.62%;逐格倒流节水和冷却水的重复或循环利用,分别占总节水量的25.18%和23.09%(22.18%+0.91%)。通过水网系统优化后,年节约新鲜水109.6×104t,每万米布节约新鲜水365t。
1.2案例二
某公司[4]年产15000万m织物,经图1和图2所示水网系统改造后(图中虚线表示改造的工艺),取得节水效益见表2。

由表2可知,该公司通过水网系统的优化改造,节水41.1×104t/a,每万米布节水27.4t,其中,冷却水
表2水网系统改造的节水效益(t/a)

回收和冷凝水回收分别为22.3×104 t/a和l3.7×104t/a;同时,通过冷凝水回收还节约蒸汽2.28×104 t/a。
通过上述案例的分析可知,案例一的节水效果明显优于案例二,案例一的节水量为365t/万m布,而案例二节水量仅为27.4t/,万m布。究其原因,两个案例最大的区别在于中水回用及逐格倒流节水技术的应用范围。案例一通过中水回用节约新鲜水50×104t/a,而其逐格倒流节水技术的应用范围以及所取得的节水效益也较大。在案例二中,仅将漂白工序后段废水和冷堆前退漂后段水回用于上一道工序,其通过逐格倒流节水技术节约水量仅5.1×104t/a,而案例一却高达27.6×104t/a。可见中水回收和逐格倒流节水,对于印染企业的节水具有非常重要的意义。
2典型工艺流程的优化与缩短
2.1冷轧堆工艺
冷轧堆工艺包括冷轧堆前处理和冷轧堆染色,这两个工艺具有很好的节水节电效益。冷轧堆前处理工艺节水135t/万m布[5],减排COD0.135t/万m布;而冷轧堆染色技术则在美国、欧美、日本和香港特区等发达国家和地区被广泛采用[6]。
2.1.1冷轧堆前处理工艺
(1)某印染厂前处理退浆、煮练、漂白3道工序,每条生产线平均生产用水量为46.5t/h,消耗蒸汽量为3.77t/h。通过大量的实践,将传统的三步法工艺改为冷轧堆前处理工艺,每条生产线的平均生产用水量为24t/h,蒸汽消耗量为2.25t/h,比传统工艺用水量节省22.5t/h,蒸汽消耗量减少1.52t/h。目前,4条生产线采用冷堆一步法工艺,比传统工艺节水45.4万t/a,每万米布节水约137.6t;比传统工艺节约蒸汽3.07万t/a,每万米布节汽约9.29t。
(2)有文献[6]指出,冷堆法比退煮漂三步法节水47.8%,每万米布节水约163t;有的文献则认为冷堆工艺比传统退煮漂工艺节水52%。某公司以灯芯绒为主产品,应用冷轧堆前处理一步法,全年可节l3.5万t[9]。
2.1.2冷轧堆染色工艺
(1)浙江某公司为配合冷轧堆染色工艺的开发,投资37万欧元从德国引进2台寇司德冷堆染色机。通过生产实践证明,该工艺较传统的连续轧染工艺,每年可节省蒸汽3050t,每万米布节汽约7.9t;节约用水48000t,每万米布节水约125t。
(2)陈胜慧等[8]通过实际的成本核算发现,冷轧堆染色工艺生产1t产品所耗的水量仅约传统工艺的10%,见表3。

(3)某公司以灯芯绒为主产品,采用活性染料冷轧堆染色全年节水4万t[9]。
2.2高效精练酶一浴一步工艺
高效精练酶一浴一步工艺取代传统的退浆一煮练一漂白工序,克服了原工艺消耗高、效率低的缺点,工艺流程短,污染物排放少,综合成本低,节能环保。
工作液配比/(g/L)[10]
双氧水(100%) 12~14
高效精练酶 25~30
精练渗透剂 5~8
高效精练酶一浴一步工艺流程
工作液加热升温至50—60℃,化料→浸轧(带液率80%~100%) →汽蒸(98~102℃,60~75min)→热水洗(95~98℃) →二次水洗(60~65℃)
锦州宏丰印染厂有限公司采用该工艺后节水效果明显(见表4)。

2.3湿布丝光工艺
(1)山东鲁泰纺织股份有限公司[11]采用湿布丝光工艺后,相比传统的干布丝光工艺,可节省烘筒蒸汽1.76t/万m布;2台漂白机节省蒸汽22t/d(以每日加工12.5万m织物计),折合人民币3762元/d,节约折合标准煤750.8t/a。
(2)山东昌邑华晨纺织印染有限公司[12]采用湿布松堆丝光工艺后,相比传统的丝光工艺,节省烘筒蒸汽2.2t/万m布,月产纯棉布240万m,每月可节省蒸汽528t。
2.4湿热丝光工艺
LMA125型高速直辊布铗丝光机上实施湿布丝光工艺,耗水0.9m3/km织物,耗汽0.634t/km织物。按年生产2000万m丝光布计,可节水20400t,即节汽4420t[2],即节水10.2t/万m布,节汽2.21t/万m布。
2.5机织物退染一浴法工艺
石狮市万峰盛漂染织造有限公司将传统的退浆→染色→还原清洗三浴法和退浆→染色二浴法改造成退染→浴法工艺[12]引,每万米布用水量从70~90t降到了35~45t,节约用水量50%左右;排污费用节约50%;每缸布染色时间从7~8h缩短到4~5h,缩短加工时间4o%~50%,同等设备增加生产量80%~90%;每万m布节约用煤为30%~40%,节约用电40%~50%,劳动力成本降低20%左右。
机织物退染一浴法工艺流程:
染料+机织物坯布→加入阴离子型退浆剂(1%~4%omf)+防裂纱(1%~2%omf)+阴E离子表面活性剂(1%~3%omf) →升温至85℃,保温10min加0~0.5%冰醋酸一水浴加热至105℃,保温40min降温至80℃
2.6练染同浴工艺
(1)绍兴县永盛练染公司把原先6道工序中的前5道合在一起完成,实现练染同浴工艺。使用新工艺后,该公司平均每染一缸布,排污由12t减为4~6t,排污量减少40%~60%;用电由160kWh减少为100kwh;蒸汽用量由1.5t降为1.1~1.2t,而且生产用时减少2h,提高了生产效率。
(2)李颖君等[14]得出练染同浴工艺与传统练一漂一染色工艺的能耗比见表5。
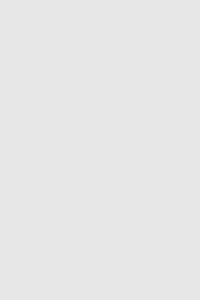
2.7短流程湿蒸染色工艺
活性染料常用轧一烘.轧一蒸法染色,连续生产效率高,但流程长、能耗高。某公司利用短流程湿蒸染色技术对传统工艺改进后,水量减少了约20%,蒸汽耗量降低15%~20%,染色的水洗过程年节省水16000t,节约蒸汽2570t。
2.8涂料染色与涂料印花
(1)涂料染色在节能降耗、减少污染物排放等方面有突破性进展,与传统染色工艺相比,节约染料/涂料20%,助剂52%(尤其是减少90%以上的染色污水的排放),烧碱95%以上,盐100%,电3l%,蒸汽30%,节水50%以上(在染色过程节水94.8%,考虑涂料染色产品后道成衣水洗用水),节省占地面积65%。与传统连续轧染相比,某公司采用新型涂料染色后节水101t/,万m布[15]。
$False$
[11]梁政佰,张战旗,于滨,等.刍议印染厂节能降耗[J].印染,2010,36(15):33-37.
[12]张子仲.棉织物布铗松堆丝光[J].印染,2008,34(11):14—15.
[13]李接代.机织物退染同浴工艺:中国,CN101476249A[P].2009—01-07.
[14]李颖君,臧蕴,张庆.高效节能的针织物练染同浴工艺[J].印染,2009,35(16):21-23.
[15]陈立秋.染整湿加工的节水技术(2)[J].染整技术,2008,30(9):4548.